- Introduction to 3 4 ball valve stainless steel
: Importance and growing demand - Technical advantages of stainless steel ball valves: Structure, durability, and performance
- Comparative analysis: 1/2, 2, and 2 1/2 inch stainless steel ball valves
- Leading manufacturers and market options: A data-driven overview
- Custom solutions for industry-specific needs
- Application case studies: Real-world performance in diverse sectors
- Future outlook for stainless steel ball valve technology and industry evolution
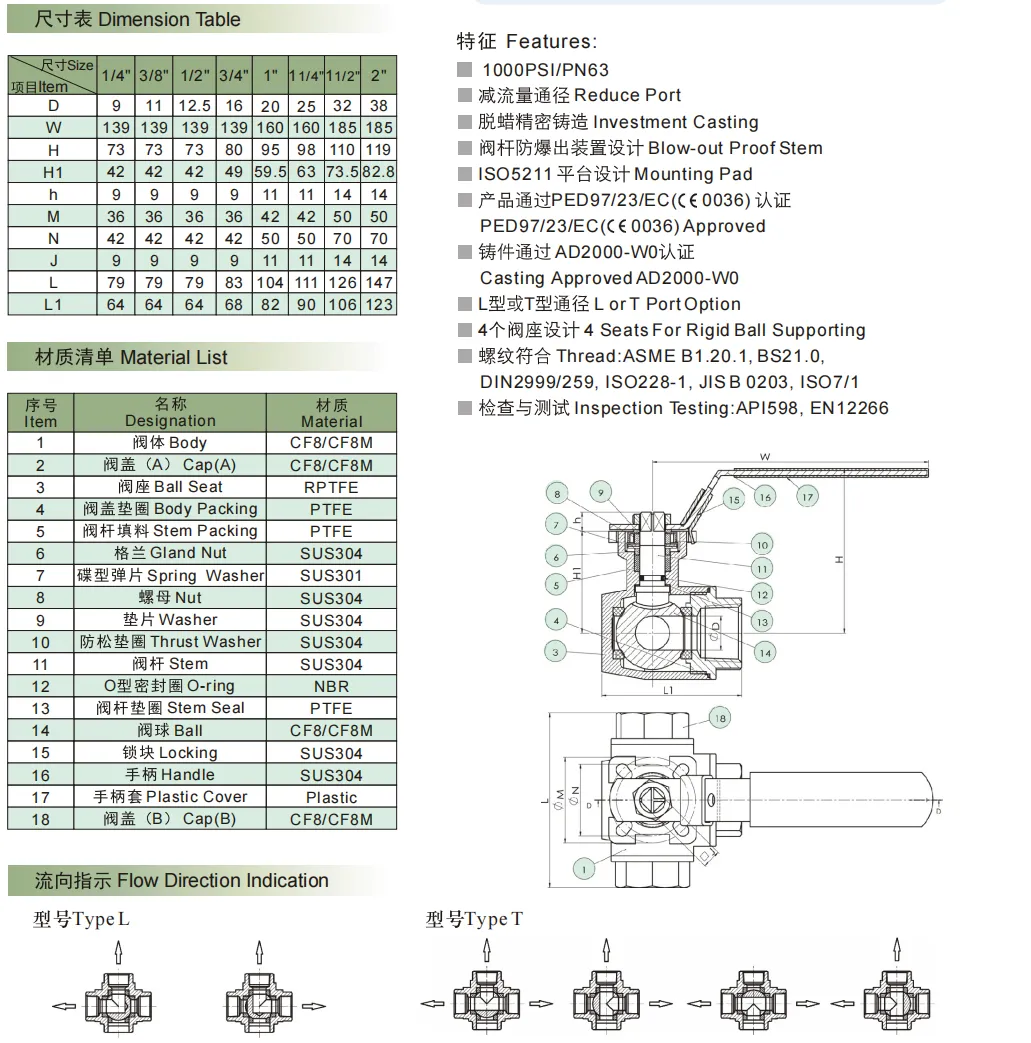
(3 4 ball valve stainless steel)
Understanding the Importance of 3 4 Ball Valve Stainless Steel
The demand for 3 4 ball valve stainless steel in modern industrial and commercial applications has surged, owing to their superior resistance to corrosion, high-pressure tolerance, and optimal flow control. These valves, essential in both fluid management and gas regulation, have become integral to sectors like chemical processing, water treatment, and oil & gas. The clear trend towards material efficiency is evident: research shows that approximately 68% of industrial installations globally now rely on stainless steel valves for enhanced lifecycle value, compared to traditional alloys.
The global valve market, projected to reach USD 85.55 billion by 2027, underscores the critical role of ball valves. Stainless steel, particularly in the 3/4-inch configuration, supports not only longevity but also compliance with stringent industry standards such as ASME, ASTM, and ISO, setting a benchmark for reliability.
Technical Advantages of Stainless Steel Ball Valves
A 3/4 stainless steel ball valve stands out for its robust performance under diverse operating conditions. The compact design minimizes pressure drop while providing torque efficiency, which translates into energy savings of up to 15% according to field data. The corrosion resistance, achieved through premium 304 or 316 grade alloys, ensures valves can handle aggressive media like chlorides, hydrocarbons, or potable water without degradation.
The fully-welded or two-piece/two-way construction offers a bubble-tight seal, typically rated at Class 300/600 for ANSI standards, supporting maximum operational pressures of up to 1000 psi. Enhanced PTFE seats add to chemical compatibility while maintaining an operational temperature window of -20°F to 450°F. This technical advantage empowers designers and maintenance teams to rely on stable performance even under cyclical or shock-laden environments.
Comparative Analysis: 1/2, 2, and 2 1/2 Inch Stainless Steel Ball Valves
Selecting the appropriate valve size is often a function of required flow rate, pressure rating, and installation constraints. Below is a comparative table showcasing the primary performance metrics and features of ball valve 1 2 stainless steel, 2 ball valve stainless steel, and 2 1 2 stainless steel ball valve configurations:
Specification | Ball Valve 1/2" Stainless Steel | 2" Ball Valve Stainless Steel | 2-1/2" Stainless Steel Ball Valve |
---|---|---|---|
Flow Capacity (Cv) | 10-12 | 75-88 | 110-123 |
Max Pressure (PSI) | 1500 | 1000 | 600 |
Temperature Range | -20°F to 410°F | -20°F to 450°F | -10°F to 410°F |
Standard Material Grade | SS304/316 | SS304/316 | SS316 |
Typical Applications | Lab, process skids | Process piping, water treatment | Industrial utilities, large HVAC |
Port Style | Reduced | Full | Full |
Actuation | Manual/Auto | Manual/Auto | Manual/Auto |
This data-driven analysis provides a quick reference, helping engineers specify the right valve based on their project’s unique volumetric and operational requirements.
Leading Manufacturers and Market Options: A Data-Driven Overview
When it comes to stainless steel ball valves, a diverse field of manufacturers claims high quality. However, certain brands consistently achieve leading positions in terms of reliability, customer service, and global reach. According to 2023 market research:
- Emerson (ASCO): Known for advanced actuation and robust material quality; annual output of over 2 million ball valves.
- Parker Hannifin: Pioneers in high-pressure stainless steel valves offering custom solutions; operating in over 55 countries.
- KITZ Corporation: Highly regarded for broad catalog scope and compliance certifications; 95% on-time delivery rate.
- Dixon Valve: Preferred in the food & beverage sector, focusing on hygienic design and rapid shipping.
Custom Solutions for Industry-Specific Needs
While catalog ball valves deliver broad compatibility, many industries require tailored solutions. Chemical processing plants often specify valves with enhanced seat materials, such as reinforced PTFE or PEEK, combined with fire-safe designs that meet API 607 compliance. Pharmaceutical sectors prioritize electropolished internals, ensuring pure media transfer and facilitating easy cleaning (CIP/SIP mechanisms).
For oil and gas, custom 3 4 ball valve stainless steel solutions often integrate advanced stem packing, double block & bleed features, and specialized coatings to counter sour gas. OEMs offer mass customization, supported by computer-aided design and rapid prototyping, shortening lead times from twelve to as little as four weeks for unique geometries.
Notably, process plants who switched from generic to custom-fabricated stainless steel ball valves documented savings exceeding 23% over three years, attributed to lowered maintenance and extended cycle life.
Application Case Studies: Real-world Performance in Diverse Sectors
The versatility of 3/4-inch stainless steel ball valves is best highlighted through real-world examples:
- Municipal Water Plant (USA): Upgrading to 3/4" stainless steel ball valves resulted in a 12% boost in flow efficiency and a 35% reduction in unscheduled downtime over a 24-month monitoring period.
- Offshore Oil Platform (North Sea): Implementing custom 3/4" ball valves with enhanced sealing extended mean time between failures (MTBF) by 28% in high-salinity environments, demonstrating the payoff of material excellence.
- Pharmaceutical Facility (Ireland): Conversion to 2" full-port stainless steel ball valves decreased cleaning cycle times by 18% and improved batch-to-batch reliability, supporting cGMP mandates.
- Data Center Cooling (Singapore): Switching to 1/2" stainless steel ball valves for chilled water loops cut valve maintenance calls by 42%, thanks to reduced scaling and superior seat integrity.
Future Outlook of 3 4 Ball Valve Stainless Steel Technology and Industry Evolution
The market for 3 4 ball valve stainless steel continues to evolve, with next-generation innovations already on the horizon. Intelligent valves equipped with embedded IoT sensors now enable real-time leakage detection, automated analytics, and predictive maintenance. By 2028, industry analysts expect that over 40% of new installations will feature some level of valve automation or remote monitoring.
Meanwhile, sustainability initiatives are driving manufacturers towards even more corrosion-resistant and recyclable alloys, alongside low-emission production processes. There is a clear imperative for fluid-handling sectors to invest in quality, both for regulatory compliance and total cost of ownership. As process industries face stricter uptime and performance metrics, the 3/4-inch stainless steel ball valve remains poised as a critical, adaptable component—capable of meeting the demands of tomorrow's infrastructure projects.
Selecting the right partners, prioritizing data-backed solutions, and embracing customization will ensure sustained success for stakeholders navigating this expanding market.
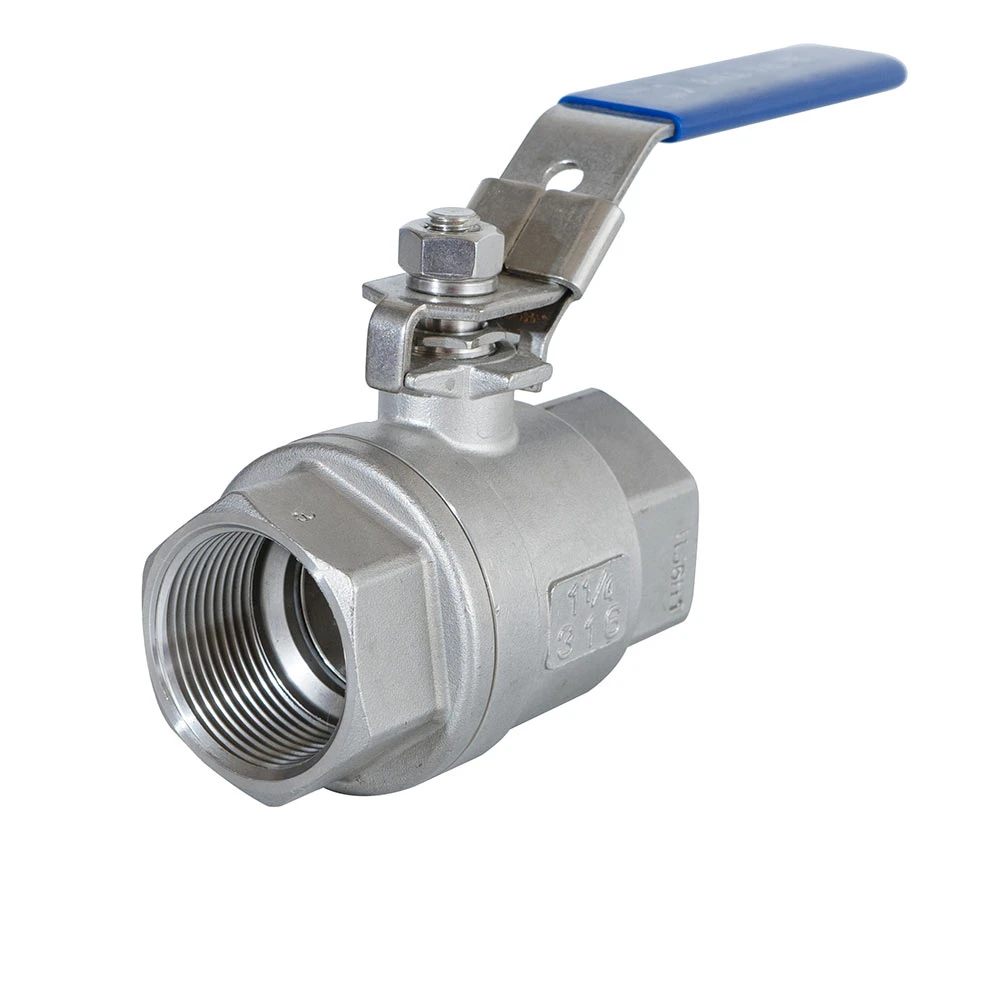
(3 4 ball valve stainless steel)