- Introduction to 2 Pipe Strainer: Definition and Overview
- The Role of Strainers in Piping Systems
- Technical Advantages of Modern Pipe Strainers
- Comparative Analysis: Leading Manufacturers
- Customization Options for Pipe Strainers
- Application Case Studies: Real-World Implementations
- Choosing the Right 2 Pipe Strainer for Your System
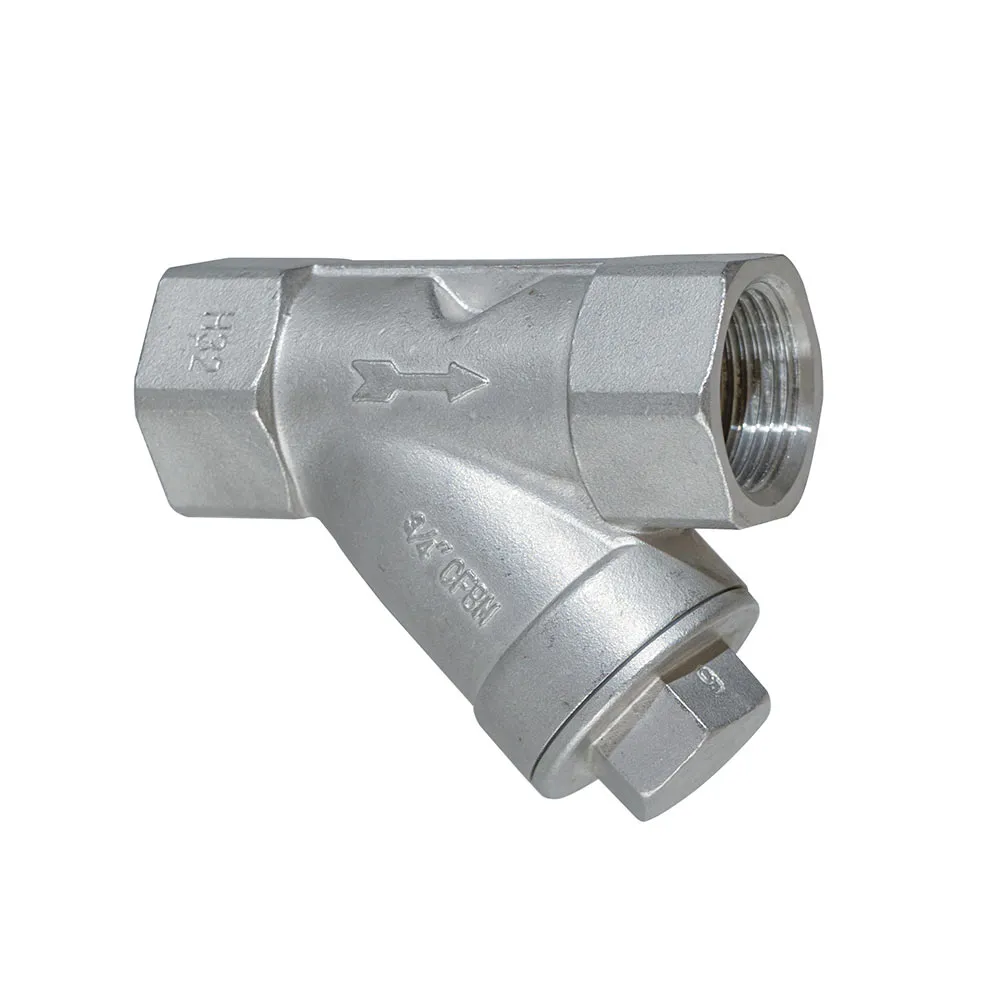
(2 pipe strainer)
Introduction to 2 Pipe Strainer: Definition and Overview
In industrial fluid handling, a 2 pipe strainer
is an essential filtration component that protects equipment by capturing foreign particles from fluid flow. It is especially crucial in systems where solids or debris can damage downstream machinery, such as pumps, valves, and heat exchangers. Whether used in water treatment, chemical processing, or HVAC applications, this device is engineered to optimize flow without sacrificing filtration efficiency. The principal variations, including the water pipe strainer, pipe y strainer, and stainless steel pipe strainer, enable system designers to tailor filtration to the needs of specific liquids, temperatures, and pressure ratings. As industries place increasing emphasis on system longevity and operational integrity, reliable strainers have become paramount.
The Role of Strainers in Piping Systems
Strainers play a proactive role in safeguarding complex piping networks. According to the Industrial Filtration Report 2023, contamination is responsible for up to 70% of unscheduled maintenance in process industries. The integration of a high-performance strainer can reduce equipment failure by as much as 50%. These filters not only capture rust, scale, and suspended solids but also prevent system-wide pressure drops. Water pipe strainers, for instance, remove sand and sediment from municipal inflow, ensuring potable water clarity and protecting critical valves. The pipe y strainer utilizes a compact, angular body design, which facilitates easier debris removal and minimizes fluid turbulence. Stainless steel pipe strainers are utilized in corrosive or high-temperature environments, where material durability is non-negotiable. The effectiveness of these filtration devices results in energy savings, reduced operational costs, and safe, compliant system performance.
Technical Advantages of Modern Pipe Strainers
The evolution of pipe strainer technology has significantly enhanced system reliability. Modern strainers are constructed from advanced alloys and polymers, providing up to 20% greater pressure resistance compared to legacy models. The mesh or perforated screens inside these strainers can be engineered to filter as fine as 10 microns, accommodating a broad spectrum of industrial needs. For example, stainless steel pipe strainers maintain structural integrity at temperatures exceeding 400°F (204°C), withstanding aggressive chemical agents. Below is a technical comparison of key strainer types used across industries:
Type | Maximum Pressure (psi) | Temperature Range (°F) | Filtration Fineness (microns) | Material | Corrosion Resistance |
---|---|---|---|---|---|
Water Pipe Strainer | 250 | 32–180 | 50–500 | Brass/Bronze | Moderate |
Pipe Y Strainer | 400 | -20–400 | 20–400 | Cast Iron/Steel | High |
Stainless Steel Pipe Strainer | 600 | -40–800 | 10–300 | 304/316 SS | Excellent |
The technical superiority of contemporary strainers ensures minimal maintenance downtime, extended equipment service life, and increased overall process efficiency.
Comparative Analysis: Leading Manufacturers
Selecting a trusted manufacturer is critical for consistency and quality assurance. Industry research indicates that the three most reputable brands in the North American and European pipe strainer markets are Eaton, Spirax Sarco, and Mueller Steam Specialty. Differences lie in manufacturing precision, warranty offers, customization latitude, and global distribution networks. In a recent buyer survey (IFN 2024), Eaton received high marks for product innovation and after-sales service, while Spirax Sarco led in operational diversity, offering over 250 unique strainer configurations. Mueller’s competitive edge stems from expedited shipment and large-inventory redundancy, minimizing lead times. The table below summarizes key comparisons among these industry leaders:
Manufacturer | Warranty (Years) | No. of Model Variants | Customization Level | Global Service | Market Share (%) |
---|---|---|---|---|---|
Eaton | 5 | 150+ | High | Yes | 32.5 |
Spirax Sarco | 3 | 250+ | Very High | Yes | 27.4 |
Mueller Steam Specialty | 2 | 100+ | Moderate | Limited | 21.6 |
This data-driven analysis enables purchasing managers and engineers to make informed decisions based on performance metrics and service reliability.
Customization Options for Pipe Strainers
Today’s fluid systems often require bespoke solutions to satisfy stringent operational and environmental standards. Leading suppliers provide a range of customization options for water pipe strainer, pipe y strainer, and stainless steel pipe strainer products. Engineers may specify custom mesh counts, which can be tailored for ultra-fine or coarse particulates depending on process requirements. Housing materials can be selected for compatibility with caustic chemicals, potable water, or high-purity pharmaceuticals. Additionally, pressure ratings are upgradable, allowing use in severe applications such as offshore drilling or hot-water loops in district heating. Optional features include pressure taps, drain valves, and magnet-assisted screens for magnetic particle capture. The flexible design process incorporates full CAD modeling, finite element analysis, and prototype validation. As a result, each strainer is aligned precisely with the system’s anticipated flow dynamics and maintenance intervals, reducing unnecessary system interventions and lifecycle costs.
Application Case Studies: Real-World Implementations
To illustrate the practical impact of efficient strainers, consider several diverse applications. In a 2022 municipal drinking water facility retrofit, the integration of stainless steel pipe strainers with 50-micron filtration decreased downstream valve replacements by 43% over a 12-month period. Similarly, a petrochemical plant utilizing pipe y strainers in glycol lines reported clogging incidents reduced from 11 cycles/year to 2 cycles/year, representing a 500% improvement in uptime. In food processing, water pipe strainers with FDA-certified elastomer seals have enabled companies to meet both regulatory standards and operational targets for particulate contamination. Furthermore, in power generation cooling towers, high-flow pipe strainers manufactured from duplex stainless steel have extended heat exchanger service intervals from quarterly to biannual, substantially lowering maintenance labor costs. These examples demonstrate that the correct selection and installation of strainers not only protect vital assets but also contribute to operational efficiency and regulatory compliance.
Choosing the Right 2 Pipe Strainer for Your System
Selecting an appropriate 2 pipe strainer begins with a comprehensive assessment of system parameters: flow rate, line size, operating temperature, and type of contaminants. Notably, industries with aggressive process media or elevated hygiene requirements benefit most from stainless steel pipe strainer designs, while pipe y strainer configurations are preferred where compactness and ease of cleaning are priorities. Sizing the strainer correctly is vital; an undersized strainer can cause excessive pressure drop, while an oversized unit might fail to capture fine particulates efficiently. Maintenance practices should incorporate routine inspection and screen cleaning schedules, tailored to process variability and criticality. By leveraging manufacturer specifications, recent advances in strainer technology, and application-specific customization, operators can optimize both filtration and fluid dynamics. Prioritizing durability, ease of servicing, and compliance ensures that a well-chosen 2 pipe strainer will provide reliable, long-term protection for valuable system components.
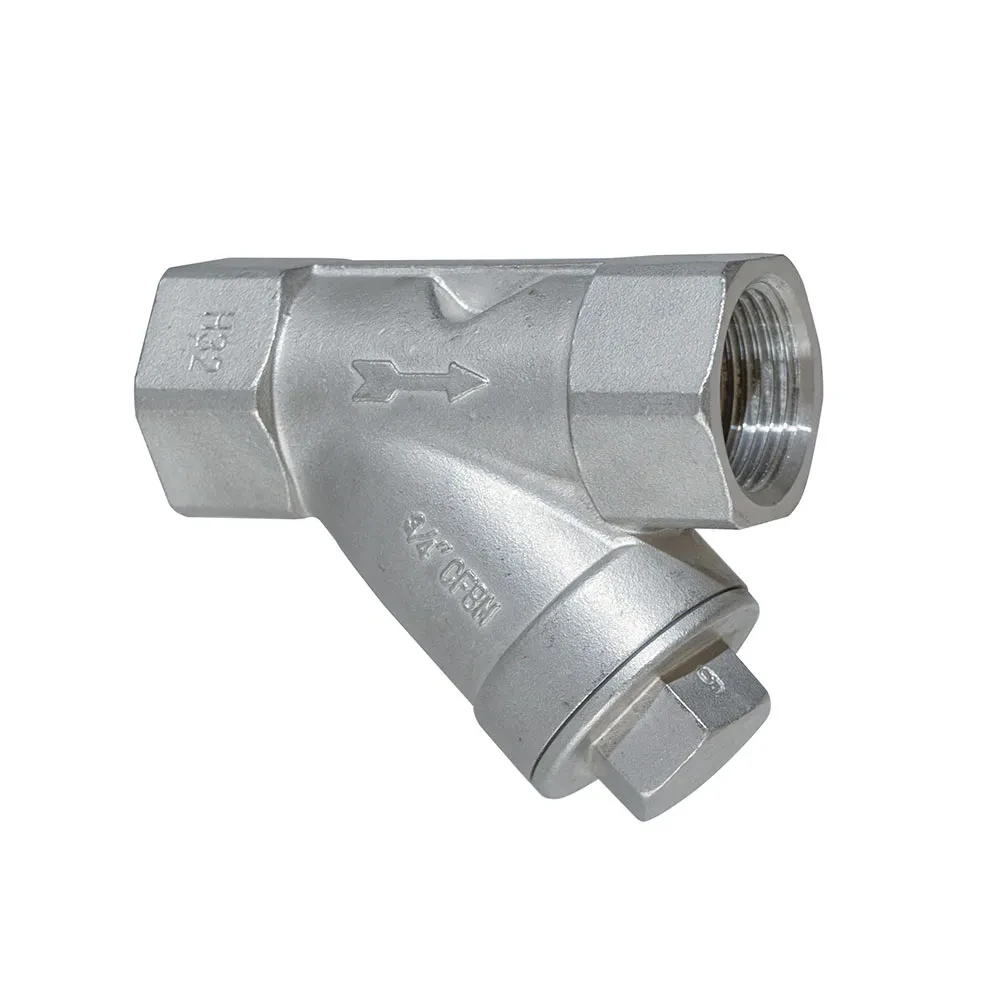
(2 pipe strainer)