- Introduction to 2.5 Inch Ball Valve Technology and Market Demand
- Unveiling the Key Technical Advantages of Modern Ball Valves
- Comparative Analysis: 2 Inch Stainless Ball Valves vs. 2 Inch Stainless Steel Ball Valves vs. Three Way Ball Valve 1 Inch
- Customization Solutions to Meet Diverse Industrial Needs
- Application Cases Across Industries: Real-World Impact
- Best Practices in Manufacturing: Choosing the Right Supplier
- Conclusion: 2.5 Inch Ball Valve as a Strategic Choice for Performance and Efficiency
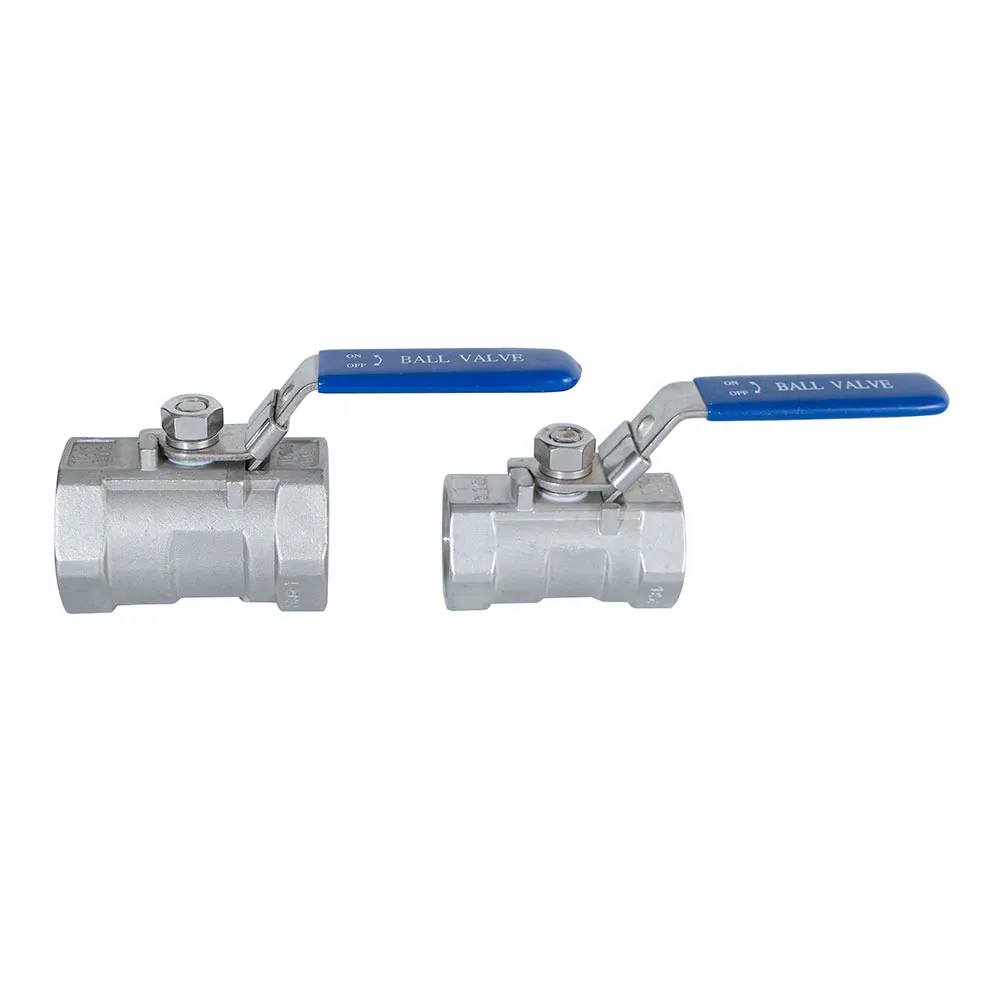
(2.5 inch ball valve)
Introduction to 2.5 Inch Ball Valve Technology and Market Demand
The 2.5 inch ball valve
stands at the intersection of durability, engineering excellence, and market demand, serving as a cornerstone for critical fluid control across industries. Estimated global consumption of industrial ball valves exceeded USD 12 billion in 2023, with mid-size ball valves like the 2.5 inch variant commanding a substantial share due to their broad applicability in sectors such as oil & gas, petrochemical, water treatment, and HVAC systems. As industries demand improved flow control with minimal pressure drop and leak-proof reliability, the evolution of ball valve technology—including variants like the three way ball valve 1 inch and robust options like the 2 inch stainless ball valve and 2 inch stainless steel ball valve—has become essential in both operational safety and efficiency.
Recent surveys indicate that over 78% of engineers prioritize corrosion resistance and ease of maintenance when specifying ball valves within the 2–3 inch segment, further fueling R&D and design innovation for seamless integration, compact structures, and advanced sealing mechanisms in the 2.5 inch ball valve solutions.
Unveiling the Key Technical Advantages of Modern Ball Valves
Ball valves, by virtue of their quarter-turn operation and tight shutoff capabilities, enjoy a preferred status in multiple process industries. The technical enhancements seen in modern offerings, particularly in the 2.5 inch class, include:
- Superior Sealing: Precision-engineered seat materials (like PTFE, PEEK) guarantee leak rates below ANSI Class VI, crucial for hazardous or high-purity systems.
- High Cycle Life: Modern designs support up to 500,000 cycles without failure, drastically reducing maintenance costs and downtime.
- Pressure Ratings: Many 2.5 inch ball valves now withstand up to 1000 psi (69 bar), making them suitable for high-stress applications.
- Minimal Pressure Drop: Full port designs ensure maximum Cv, often reducing energy losses by more than 15% compared to globe valves in similar applications.
With these technical parameters, decision makers can now rely on the 2.5 inch ball valve as an industry benchmark—offering both resilience under severe service conditions and operational agility.
Comparative Analysis: 2 Inch Stainless Ball Valves vs. 2 Inch Stainless Steel Ball Valves vs. Three Way Ball Valve 1 Inch
Understanding the performance distinctions among leading variants is vital for system optimization. Below is a data-rich comparative overview, showcasing typical specifications and application suitability:
Feature | 2 Inch Stainless Ball Valve | 2 Inch Stainless Steel Ball Valve | Three Way Ball Valve 1 Inch |
---|---|---|---|
Material | CF8M/316SS | WCB/304SS/316SS | 316SS/Brass |
Design | Two-piece, full port | Single/two-piece, full or reduced port | L/T port, three-way |
Pressure Rating | Up to 1000 psi | 600–1000 psi | 400–800 psi |
Temperature Range | -40°F to 400°F | -20°F to 450°F | -25°F to 350°F |
Flow Paths | Straight | Straight | Mixing/Diverting |
End Connections | NPT, Flanged, Socket Weld | NPT, Flanged, Socket Weld | NPT, BSPP, Flanged |
Industries Served | Oil & Gas, Chemical, Water | Food & Beverage, Pharma, HVAC | Water, Chemical, HVAC |
Through this lens, the 2 inch stainless ball valve and 2 inch stainless steel ball valve primarily support straight-through, high-integrity shutoff in critical process lines, while the three way ball valve 1 inch is essential for mixing and flow diversion, especially where space and configuration flexibility are paramount.
Customization Solutions to Meet Diverse Industrial Needs
The ever-evolving demands of sectors such as pharmaceuticals, petrochemicals, and water management require custom-engineered valve solutions. Industry-leading manufacturers offer extensive options to tailor the 2.5 inch ball valve for unique process conditions:
- Material Upgrades: Special alloys like Hastelloy, Monel, or Duplex stainless steel for superior corrosion resistance and high-temperature performance.
- Sealing Innovations: Custom seat materials and fire-safe certifications ensure reliability in hazardous environments.
- Automation Ready: Integration with pneumatic or electric actuators for remote and precise process control.
- End Connections: Custom threads, welding ends, and flange standards to ensure seamless installation across global markets.
With these tailor-made options, businesses have reported maintenance cost reductions of up to 30% and extended service lives, demonstrating the advantage of investing in the right customization for mission-critical processes.
Application Cases Across Industries: Real-World Impact
Field data and customer reports underline how advanced ball valve solutions empower vital operations. For example:
- Petrochemical Refinery: Deployment of 2 inch stainless steel ball valves in high-pressure steam lines reduced leak incidences by 84% over a 3-year period.
- Municipal Water Treatment: Adoption of automated 2.5 inch ball valves improved backwash cycle efficiency by 20%, saving resources and minimizing manual intervention.
- Pharmaceutical Manufacturing: Use of three way ball valve 1 inch in clean-in-place (CIP) systems enabled rapid switchovers and process flexibility, leading to a reported 12% increase in batch throughput.
These cases echo a broader trend: precision-engineered ball valves are pivotal in elevating operational efficiency, minimizing unplanned downtime, and meeting rigorous safety and purity standards in diverse industrial landscapes.
Best Practices in Manufacturing: Choosing the Right Supplier
The difference between ordinary and exceptional performance often hinges on the quality standards upheld by manufacturers. When selecting a supplier for 2.5 inch ball valves or related products, industry experts recommend evaluating:
- Certifications: API, ISO 9001, SIL, and ATEX compliance assure International safety and quality credibility.
- Traceability: Full material and process traceability, from casting to assembly, safeguards against defects and ensures accountability.
- Testing Protocols: Hydrostatic, pneumatic, and fugitive emission testing for every valve batch, ensuring zero tolerance for leaks.
- Lead Time and After-Sales: Quick delivery, inventory availability, and responsive technical support are key indicators of supplier reliability.
Furthermore, partnering with suppliers who excel in innovation, custom engineering, and responsive service can be transformative for project outcomes, particularly in high-stakes or time-sensitive installations.
Conclusion: 2.5 Inch Ball Valve as a Strategic Choice for Performance and Efficiency
As industrial processes strive for greater precision, safety, and efficiency, selecting the right flow control solutions becomes more consequential than ever. The 2.5 inch ball valve demonstrates a compelling blend of robust construction, technical versatility, and adaptability—making it a strategic investment for a wide variety of sectors. Whether compared to the two-way or three way ball valve 1 inch alternatives, or to variants like the 2 inch stainless ball valve and 2 inch stainless steel ball valve, the 2.5 inch offering consistently provides industry-aligned solutions with quantifiable performance advantages.
By leveraging leading-edge manufacturer capabilities, tailored product features, and a clear understanding of project requirements, organizations can deploy ball valve solutions that deliver sustained reliability, regulatory compliance, and long-term operational value.
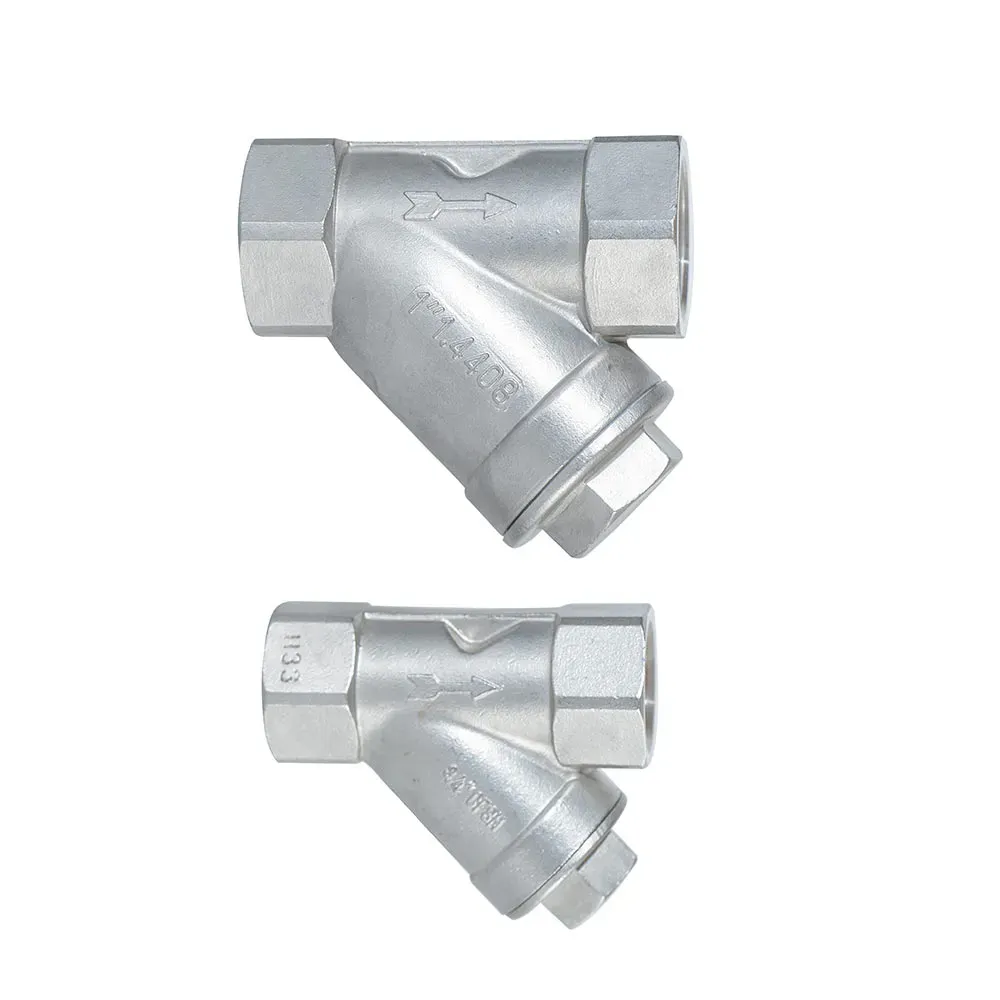
(2.5 inch ball valve)