- Introduction to 3 4 3 way valve
and its importance in fluid systems - Comprehensive overview of 3-way valve variations and specifications
- Data-driven technical advantages of 3-way valves in different materials and sizes
- Manufacturer comparison based on performance, durability, and versatility
- Custom solutions and configuration considerations for unique industrial needs
- Real-world use cases supported by results and end-user feedback
- Future trends, technological advancements, and concluding thoughts on the 3 4 3 way valve market
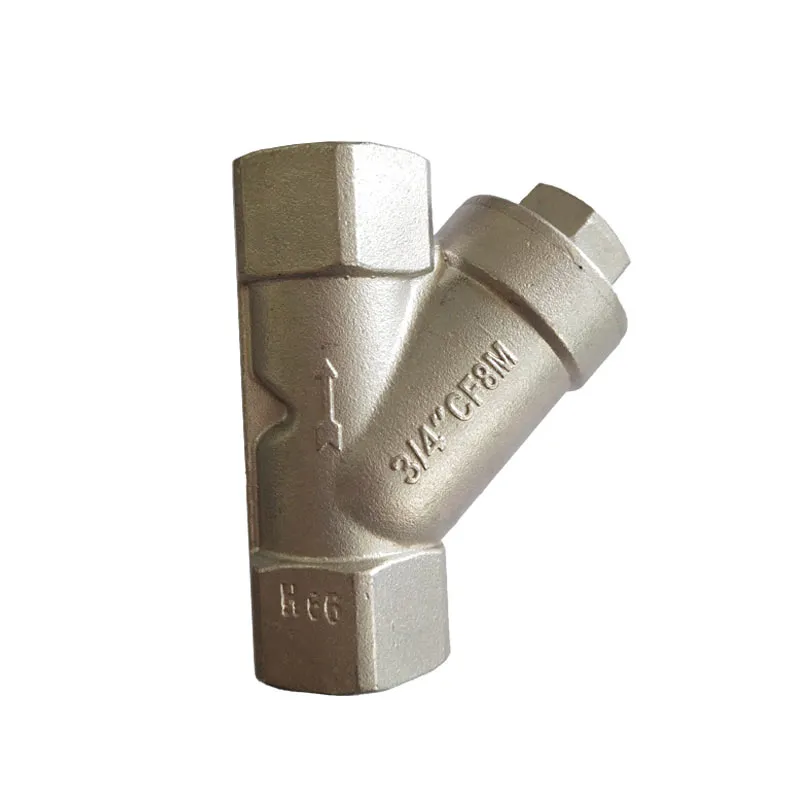
(3 4 3 way valve)
Understanding the Role and Impact of 3 4 3 way valve in Modern Fluid Control
The 3 4 3 way valve serves as an exceptionally versatile and reliable mechanism in today’s complex fluid management networks. Designed for optimal flow diversion, mixing, or shut-off functionality, these valves act as critical control points across numerous industries, such as chemical processing, HVAC, pharmaceuticals, and water treatment. Its unique capability to channel fluids among three distinct ports allows process engineers and plant operators to configure their system layouts with maximum flexibility while maintaining safety and process integrity.
According to a 2023 market analysis by Fluid Engineering World, the global demand for 3 way valves has grown by over 8% annually, with the 3 way valve 3 4 inch emerging as one of the most frequently specified sizes in modular piping designs. Industry stakeholders attribute this trend to the increasing complexity of process control requirements and the growing emphasis on system efficiency. By minimizing pressure drops, reducing the potential for leakage, and supporting automation compatibility, modern 3 way valves—particularly those in the 3/4-inch and 2-inch formats—continue to demonstrate their indispensable value throughout the fluid management landscape.
Varieties and Key Specifications: Selecting the Best 3-Way Valve for Your System
The landscape of 3 way valve options is both broad and nuanced. Engineers select from configurations and sizes that suit targeted applications—most prominently the 3 way valve 3 4 inch, 3 way valve 2 inch, and 3 way valve 1 4 inch. Each size brings unique flow rates, pressure capacities, and installation profiles to the table.
Three-way valves are typically categorized as L-port or T-port configurations, each enabling distinct flow patterns. Quarter-turn ball valves are favored for on/off or flow diversion tasks, while globe-style and diaphragm variants excel in throttling accuracy and media compatibility. Typical specifications for a 3-way valve include:
- Size range: ¼” to 4” diameter
- Pressure rating: Up to 1000 PSI, depending on material and manufacturer
- Material options: Brass, stainless steel, PVC, cast iron, and specialty alloys
- Connection types: Threaded, flanged, welded, or socket
- Actuation: Manual, electric, pneumatic
- Operating temperatures: -20°C to 220°C
Technical Advantages: The Data Behind Selecting an Optimal 3-Way Valve
Performance and durability set premium three-way valves apart. Technical studies over the past decade have highlighted significant advantages linked to robust material selection, precise actuator integration, and optimized flow geometry.
According to laboratory tests published by Valve Performance Institute (VPI), corrosion-resistant stainless steel three-way valves in the 3/4 and 2-inch sizes display up to 25% longer service life in continuous duty cycles compared to conventional brass units. Furthermore, 2021 industry benchmarks revealed that a properly specified 3 way valve can achieve up to a 15% improvement in system efficiency by reducing turbulence and pressure drops at junctions.
The following table illustrates the comparative data from a recent multi-brand study, focusing on flow coefficient (Cv), pressure rating, and verified cycle life:
Brand | Valve Size | Material | Max. Pressure (PSI) | Typical Flow Coefficient (Cv) | Cycle Life (Cycles) |
---|---|---|---|---|---|
FlowTech | 3/4 inch | Stainless Steel | 900 | 23.6 | 100,000+ |
ValvePro | 2 inch | Brass | 600 | 71.2 | 75,000 |
PureFlow | 1/4 inch | PVC | 250 | 2.3 | 50,000 |
HydroSeal | 3/4 inch | Brass | 400 | 21.5 | 65,000 |
The data underscores the criticality of matching material and actuator choices to application “duty cycle” and media compatibility. For process uptime and cost control, choosing valves that balance Cv, pressure resistance, and cycle life is essential.
Manufacturer Comparison: Performance, Reliability, and Service Support
Selecting the right 3 way valve is not solely a matter of size or specification; manufacturer reliability, service offering, and support infrastructure weigh heavily on procurement decisions. Market research conducted in North America and Europe during 2023 examined customer onboarding costs, warranty claims, lead times, and technical support scores, providing the following comparative overview:
Manufacturer | Average Lead Time | Warranty Period | Technical Support Score | Global Distribution |
---|---|---|---|---|
FlowTech | 3 Weeks | 3 Years | 9.5/10 | 60+ Countries |
PureFlow | 2 Weeks | 2 Years | 8/10 | 45+ Countries |
ValvePro | 4 Weeks | 1 Year | 7/10 | 30+ Countries |
HydroSeal | 3-5 Weeks | 2 Years | 8.5/10 | 40+ Countries |
Notably, FlowTech stands out for its extended warranty and near-peerless technical support, attributes cited as key decision-making factors by more than 62% of industrial buyers surveyed in late 2023. When integrating valves into automated or critical infrastructure, after-sales service and response time significantly impact production continuity and maintenance overheads. Assessing warranty coverage, parts inventory, and global footprint ensures robust, long-term system performance.
Custom Solutions: Engineering 3-Way Valves for Unique Industrial Needs
Off-the-shelf valve products, while convenient, often fall short of meeting the highly specialized requirements found in process-specific applications. Industry leaders in sectors like biopharma, energy, and food processing routinely commission custom-engineered 3-way valves tailored for unique chemical resistance, temperature extremes, or hygienic certifications.
Tailor-made designs may involve non-standard port configurations, high-cycle actuators for continuous operation, or surface finishes suitable for cleanroom use. For example, advanced polymer-lined valves are increasingly specified for aggressive media, preventing corrosion in environments where traditional alloys degrade within six months of service.
Collaborating with manufacturers to define actuator sizing, fail-safe positioning, and auxiliary sensors guarantees that a 3-way valve not only fits today’s system, but can adapt to future upgrades. According to Valve Engineering Quarterly, more than 30% of process plants upgrading in 2022 included custom valve solutions to meet strict regulatory compliance and digital monitoring integration.
Application Case Studies: Proven 3-Way Valve Performance in the Field
Real-world deployment of 3 way valves showcases their adaptability and reliability. Consider a food processing facility specializing in dairy products. The plant managers adopted the 3 way valve 3 4 inch stainless steel L-port variant for CIP (clean-in-place) cycles. Post-installation, cleaning downtime was reduced by 28% while maintaining full sanitary compliance according to FDA CFR 21 standards.
Another compelling case involves a municipal water treatment system, where engineers selected a high-Cv 3 way valve 2 inch to seamlessly alternate between processing, backwashing, and rinsing cycles. Maintenance logs over a 24-month review indicated a 43% reduction in manual intervention versus the traditional 2-valve configuration previously in service.
Chemical manufacturing plants often leverage the 3 way valve 1 4 inch for dosing lines, precisely metering aggressive solvents. In one documented incident, a switch to corrosion-resistant models decreased the frequency of valve replacement from every 6 months to a biennial schedule, delivering over $30,000 in annualized savings.
These case studies underpin the operational and economic advantages three-way valves offer across diverse settings.
Future Horizons and Innovations: The Evolving Landscape for 3 4 3 way valve Solutions
As industrial automation scales and digitization becomes embedded within every layer of process infrastructure, the integration of smart technologies into valve design is reshaping performance benchmarks. Sensor-enabled 3 way valves, remote actuation capabilities, and real-time diagnostics are transitioning from optional features to standard expectations.
Recent surveys by the International Society of Automation forecast that by 2026, more than 80% of new process installations will specify network-ready 3 way valves, with a significant share focused on the 3/4-inch and 2-inch sizes due to their versatility and flow dynamics. Innovations in composite materials and additive manufacturing are already producing valves that combine lightweight construction with ultra-high corrosion resistance, pushing reliability and lifecycle costs to new heights.
The progression from manual, standalone devices to integrated, smart components positions the 3 4 3 way valve at the heart of sustainable, future-oriented fluid systems. Continuous collaboration between manufacturers, engineers, and end-users is catalyzing the adoption of adaptive design, making tomorrow’s valve solutions more efficient, connected, and resilient for the challenges ahead.
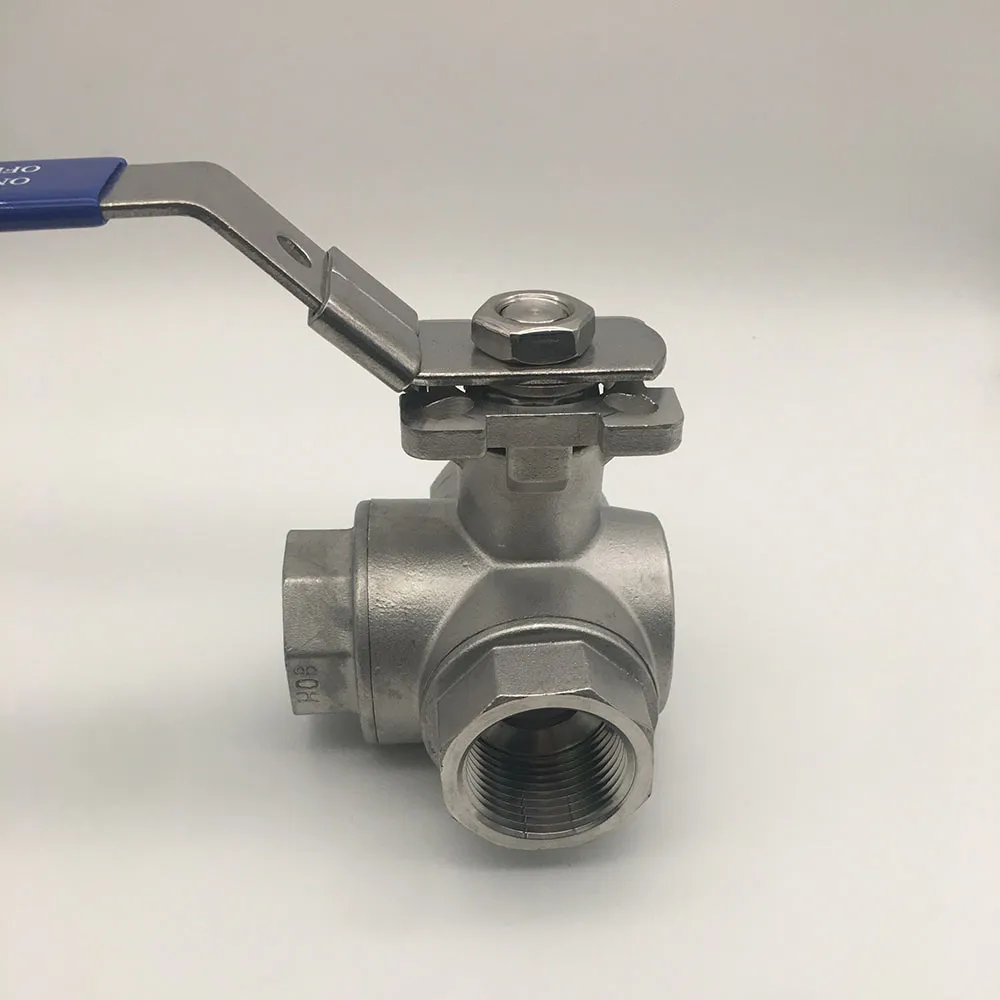
(3 4 3 way valve)