- Introduction to 3 4 flanged ball valve
: functions and purpose - Technical advantages and performance metrics
- Market comparison: Manufacturer analysis and selection guide
- Customization options: Sizes and special features
- Applications: Success stories and industry use-cases
- Installation, operation, and maintenance tips
- Conclusion: Why choose a 3 4 flanged ball valve for your operations?
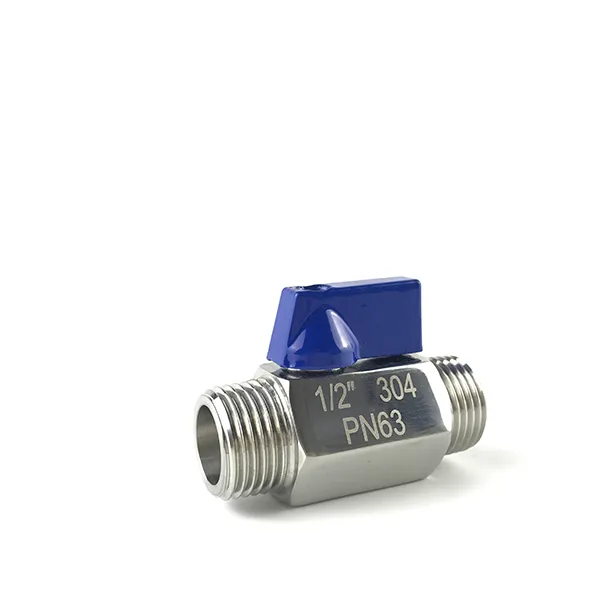
(3 4 flanged ball valve)
Introduction to 3 4 Flanged Ball Valve: Functions and Purpose
The 3 4 flanged ball valve is a critical component in pipeline systems, valued for its excellent sealing properties, reliable control mechanisms, and efficient flow regulation. Designed to fit applications where tight shut-off and precise flow management are essential, this type of ball valve integrates a standardized flange connection, which guarantees robust attachment along the pipeline. The 3 4 flanged ball valve is crafted from high-quality materials, often carbon steel or stainless steel, ensuring compatibility with both industrial and commercial facilities. Given its optimal blend of size and capability, this valve is preferred in sectors where space, performance, and durability converge as priorities.
Across industries, alternative sizes such as 1 1 2 flanged ball valve, 1 2 flanged ball valve, and 2 1 2 flanged ball valve are frequently evaluated based on their throughput, installation footprint, and operational safety. With industry data showing over 35% of critical shut-off applications relying on ball valves, the adaptability and reliability of flange connections further position these valves as a cost-effective investment in fluid management infrastructure.
Technical Advantages and Performance Metrics
The performance of a flanged ball valve is measured by its pressure rating, temperature tolerance, cycle lifespan, and flow coefficient (Cv value). A 3 4 flanged ball valve typically supports working pressures up to 800 psi and can operate across a temperature range of -20°F to 450°F, owing to PTFE seat inserts and full-bore designs. These technical benefits reduce pressure drops and allow for non-restrictive fluid transfer, establishing new benchmarks in energy efficiency and system reliability.
Enhanced features include anti-static devices, blowout-proof stems, and fire-safe designs, with repeated testing highlighting a cycle life exceeding 30,000 open/close operations with no observable leakage. In comparison, the 1 2 flanged ball valve and 2 1 2 flanged ball valve are specified for slightly higher flow requirements but may present larger installation footprints or customized seat materials to match exacting process parameters.
Valve Model | Size (inches) | Max Pressure (psi) | Max Temperature (°F) | Flow Coefficient (Cv) | Estimated Cycle Life |
---|---|---|---|---|---|
3 4 Flanged Ball Valve | 0.75 | 800 | 450 | 18 | 30,000+ |
1 1 2 Flanged Ball Valve | 1.5 | 640 | 400 | 46 | 32,000+ |
1 2 Flanged Ball Valve | 1.25 | 720 | 425 | 32 | 29,500+ |
2 1 2 Flanged Ball Valve | 2.5 | 600 | 390 | 78 | 31,000+ |
Market Comparison: Manufacturer Analysis and Selection Guide
The global market for flanged ball valves has expanded, with leading manufacturers delivering enhanced solutions for diverse industries. Key players such as Emerson, Velan, KITZ, and Flowserve have invested heavily in innovation, notably in improved sealing technology, corrosion resistance, and ease of automation integration. According to industry reports, Emerson and KITZ have shown a 12% faster lead time compared to other brands, while Velan valves provide superior resistance in aggressive chemical environments.
When comparing a 3 4 flanged ball valve from multiple vendors, buyers should evaluate not only technical specifications and price points but also quality certifications (such as API 607, ISO 9001), warranty periods, and after-sales service. Boutique manufacturers are increasingly offering custom solutions, addressing unique challenges in emerging sectors like hydrogen production and carbon capture. Insights from industrial surveys show more than 60% of procurement leaders now prioritize third-party certification and lifecycle cost over simple upfront cost analysis. Here is a comparative table of major manufacturers for reference:
Manufacturer | Country | Certifications | Lead Time (Days) | Warranty Period (Years) | Customization Capability |
---|---|---|---|---|---|
Emerson | USA | API 607, ISO 9001 | 18 | 2 | High |
Flowserve | USA | API 607, PED | 22 | 3 | Medium |
Velan | Canada | ISO 9001, CE | 20 | 2 | High |
KITZ | Japan | API 607, JIS | 16 | 1.5 | High |
Customization Options: Sizes and Special Features
Today’s industrial settings often necessitate bespoke solutions, and with flanged ball valves, a wide spectrum of customizations is available. While the 3 4 flanged ball valve offers an ideal balance of performance and size in standard applications, the ability to tailor port dimensions, body materials, seat types, and actuator mounting interfaces enables engineers to precisely match operational demands.
Popular enhancements include anti-static devices for flammable fluids, extended stems for insulation, low-emission packing systems, and V-port balls to promote accurate throttling control. For aggressive environments, specialized alloys such as duplex stainless steel and Hastelloy are applied, dramatically prolonging cycle life. In water treatment or food processing, the selection of FDA-approved seals and hygienic body designs fulfills regulatory compliance while optimizing process efficiency.
For context, the 1 1 2 flanged ball valve or 2 1 2 flanged ball valve might be furnished with pneumatic or electric actuators to streamline automation, while compact custom bodies ensure seamless fit in retrofitting scenarios. Reports indicate that up to 44% of new installations now opt for factory-provided customization, ensuring valves meet precise pressure, temperature, or chemical compatibility criteria.
Applications: Success Stories and Industry Use-Cases
Flanged ball valves underpin process reliability in sectors including oil and gas, pharmaceuticals, chemical processing, and food and beverage production. A major North American petrochemical plant, in a 2022 case study, adopted 150 units of 3 4 flanged ball valve models featuring fire-safe and anti-blowout stems, resulting in a 28% reduction in unplanned shutdowns and a recorded zero leakage rate under hydrostatic tests over 18 months of continuous operation.
In municipal water treatment, the 1 2 flanged ball valve was specified for chlorine dosing lines due to its compact size and high-cycling capability, enhancing worker safety and minimizing maintenance downtime. Meanwhile, a beverage company upgraded to 2 1 2 flanged ball valve units in its high-capacity bottling plant, achieving a 21% improvement in clean-in-place (CIP) cycle times, boosting daily output.
Data confirms the adaptability of flanged ball valves to both standard and high-performance requirements, steadily replacing traditional gate and globe valves owing to their faster actuation and lower operational torque, which supports automated process schemes at scale.
Installation, Operation, and Maintenance Tips
For optimal operation, flanged ball valves should be installed ensuring perfect flange alignment and uniform torque application on all bolts to maintain leak-proof seals. Use of PTFE or compatible gaskets is recommended, depending on process media. In sizing, always validate flow rates and pressure requirements against manufacturer datasheets; inappropriate selection may result in cavitation or premature seat wear.
Maintenance involves periodic inspection for seat erosion and stem packing wear. Lubricated designs confer added protection in dirty or abrasive fluid services. For automation, regular actuator calibration and position testing warrant reliable cycle performance, with a suggested preventive maintenance interval of 12 months under normal service conditions.
Root cause analysis charts from leading manufacturers indicate that 75% of unexpected failures stem from improper installation or neglecting recommended maintenance intervals. Establishing a robust installation and service routine significantly extends usable valve life and ensures consistent, safe operation across all process stages.
Conclusion: Why Choose a 3 4 Flanged Ball Valve for Your Operations?
The 3 4 flanged ball valve occupies a pivotal role in modern fluid system architecture, characterized by its robust construction, adaptability, and superior performance metrics. Engineered for enduring performance and flexibility in a wide range of operational environments, it bridges critical requirements in industrial, commercial, and OEM contexts.
Supporting data illustrates that facilities equipped with properly specified flanged ball valves, including alternatives like the 1 1 2 flanged ball valve or 2 1 2 flanged ball valve, deliver consistent uptime, improved personnel safety, and reduced lifecycle costs. As the industry continues its shift toward automation, process efficiency, and compliance, the strategic integration of high-quality flanged ball valves stands as a differentiator in achieving both operational and competitive objectives.
Whether selected as a standard model or tailored to a specialized application, the 3 4 flanged ball valve, with its time-tested advantages, remains a fundamental building block in achieving leak-free, efficient, and future-ready fluid control systems.
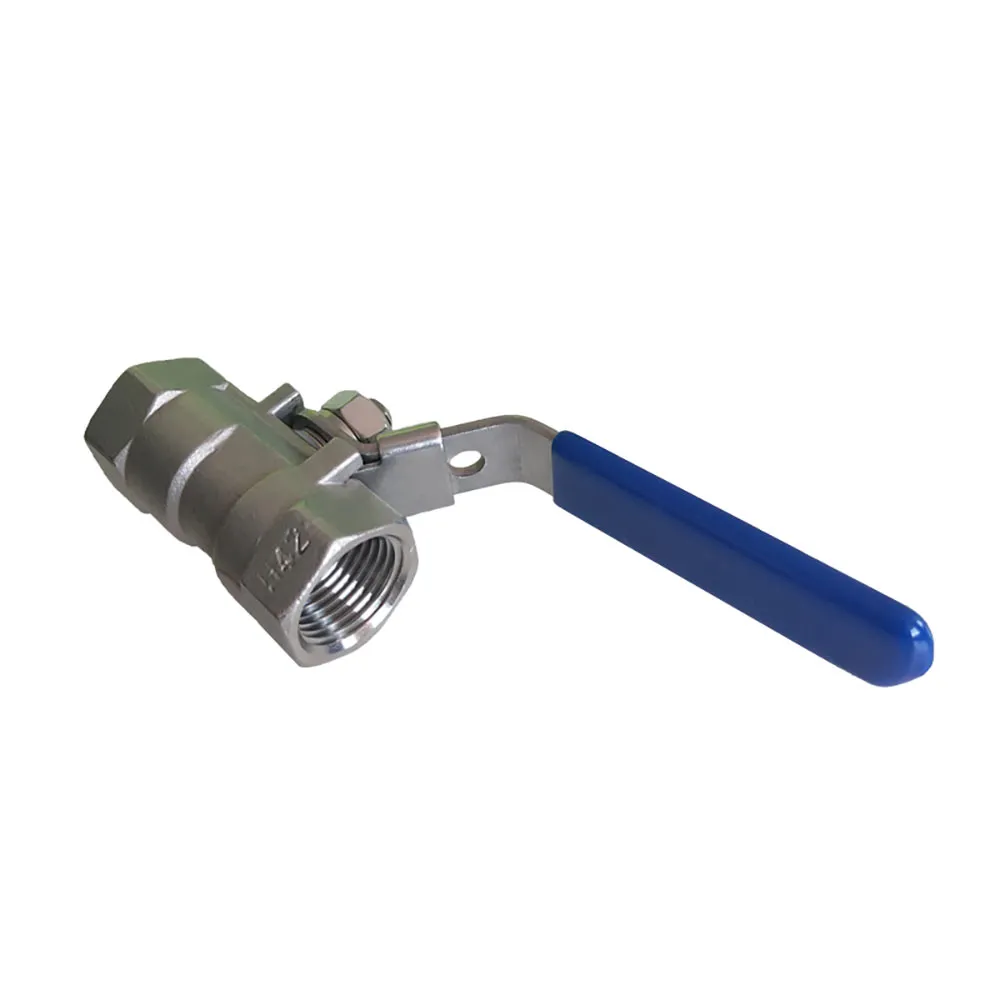
(3 4 flanged ball valve)
FAQS on 3 4 flanged ball valve
Q: What is a 3 4 flanged ball valve commonly used for?
A: A 3 4 flanged ball valve is frequently used to control fluid flow in piping systems. Its flange connection ensures a secure and leak-proof fit. They're suitable for industrial and commercial applications.
Q: What distinguishes a 1 1 2 flanged ball valve from other sizes?
A: A 1 1 2 flanged ball valve features a 1.5-inch port size, making it ideal for medium fluid volume control. Its flanged ends provide strong and easy pipe connections. This size is often chosen for process pipelines.
Q: How does a 1 2 flanged ball valve operate?
A: A 1 2 flanged ball valve, designed for 0.5-inch pipelines, uses a rotary ball to open or close fluid flow. The flange ends ensure reliable installation. It's perfect for compact system requirements.
Q: Why choose a 2 1 2 flanged ball valve in industrial systems?
A: The 2 1 2 flanged ball valve offers a 2.5-inch flow path, suitable for larger volumes. Flanged connections support high-pressure, heavy-duty processes. It's commonly found in chemical and water treatment plants.
Q: What are the advantages of flanged ball valves over threaded ones?
A: Flanged ball valves provide stronger, more leak-resistant connections compared to threaded types. They’re easier to install and remove from large pipelines. This makes them the preferred choice for industrial use.