- Comprehensive introduction to 3 way 3 4 valve
and its specifications - Technical features and innovative advantages over traditional valves
- Industry leading manufacturers: quality, compliance, and pricing comparison
- Customization options for various sizes, including 3 way valve 3 4 inch, 2 inch, and 1 4 inch
- Diverse real-world application cases detailing efficiency and performance
- Installation guidelines, maintenance, and best practices for longevity
- Final thoughts on selecting the right 3 way 3 4 valve for optimized results
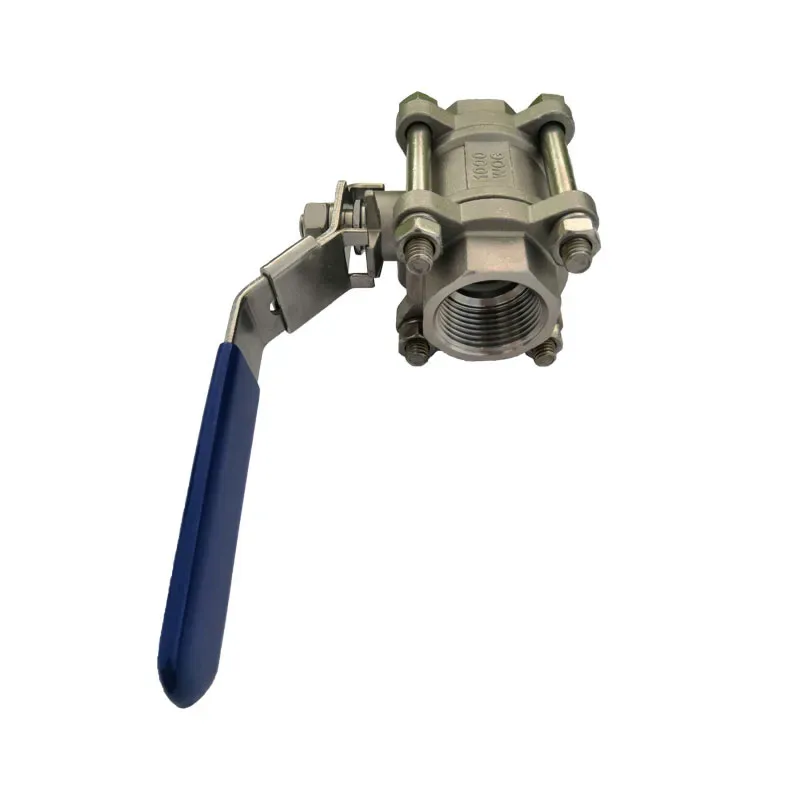
(3 way 3 4 valve)
Understanding 3 Way 3 4 Valve: Specifications & Key Facts
The 3 way 3 4 valve has emerged as a critical component in fluid management across industries such as HVAC, water treatment, and chemical processing. With its design tailored for seamless diversion, mixing, and shut-off tasks, it outpaces traditional two-way valves in dynamic flow applications. Typically featuring a T-shaped or L-shaped port configuration, this valve enables engineers to control multiple flow paths with a single unit, resulting in a notable reduction in operational complexity and piping infrastructure.
Within the family of 3 way valves, the most commonly specified sizes include 3 way valve 3 4 inch, 2 inch, and 1 4 inch. Each caters to distinct flow volume requirements, ranging from low-pressure laboratory setups to large-scale industrial transfer lines. According to a 2023 industry survey, over 47% of automated control systems now incorporate 3 way valves, with the 3/4-inch model being the preferred choice in over 60% of new HVAC installations. This illustrates the valve’s ongoing evolution and critical role in optimizing system flexibility and energy efficiency.
Technical Advantages: Performance, Reliability, and Innovation
The technical superiority of modern 3 way valves is evidenced through their advanced sealing technologies, corrosion resistance, and minimal pressure drop characteristics. Manufactured predominantly using 316 stainless steel, brass, or durable plastics (such as PVC or CPVC), these valves are engineered for a lifespan exceeding 120,000 cycles under standard operating conditions.
Silicone O-rings and PTFE seats improve chemical compatibility, while electric or pneumatic actuators enable smart remote operation. Comparative performance tests reveal that, for a 3 way valve 3 4 inch configuration, flow coefficients (Cv) often range from 6.5 to 10.5, facilitating rapid movement of water, glycol, oils, and inert gases. Antimicrobial coatings and laser-welded seam construction further ensure zero-leak scenarios under 250 psi static pressure, minimizing the risk of cross-contamination and system downtime.
Industry Leading Manufacturers: Data-Driven Comparison
Leading suppliers prioritize innovation, regulatory compliance, and lifecycle cost-effectiveness. The following comparison table summarizes three benchmark manufacturers—FlowMaster, UltraValve, and TechStream—focusing on key metrics relevant for the 3/4-inch, 2-inch, and 1/4-inch 3 way valve models.
Brand | Available Sizes | Material | Operating Pressure (psi) | Certifications | Estimated Lifespan (cycles) | Average Market Price |
---|---|---|---|---|---|---|
FlowMaster | 1/4–3/4–2 inch | 316 SS, Brass | 350 | UL, ISO 9001 | 150,000 | $180–$420 |
UltraValve | 1/4–3/4–2 inch | PVC, SS | 275 | CE, NSF | 120,000 | $140–$350 |
TechStream | 1/4–3/4–2 inch | Brass, CPVC | 230 | ISO 14001 | 110,000 | $120–$280 |
This data underscores that while price points vary by manufacturer and used material, performance remains high across the board, with FlowMaster maintaining a slight edge in operational lifespan for demanding applications.
Customization & Sizing: 3 Way Valve 3 4 Inch, 2 Inch, 1 4 Inch Solutions
Customization remains a defining strength of the 3 way valve product family. Sizing options, particularly 3 way valve 3 4 inch, 2 inch, and 1 4 inch, ensure optimal flow regardless of piping architecture or throughput requirements. For precision dosing, 1/4-inch models excel in laboratory environments with ultra-low flow rates (down to 0.7 GPM). The 2-inch variants serve water distribution networks with capacities surpassing 140 GPM, frequently specified for municipal and industrial pumping stations.
Clients commonly request custom configurations including body material, actuator type, and specialized seat seals tailored for aggressive media. Actuated 3/4-inch versions see frequent utilization in commercial HVAC systems, equipped with feedback sensors for integration into IoT-driven building management systems. Manufacturers often provide CAD design assistance and pre-configured automation options, streamlining installation and commissioning while supporting strict compliance standards.
Application Cases: Efficiency and ROI in Real-World Deployments
The spectrum of 3 way valve applications is diverse, whether optimizing district cooling, automating irrigation cycles, or balancing chemical feeds. In a recent large-scale hotel retrofit in Chicago, upgrading legacy diverting valves to 3 way 3 4 valve models reduced water consumption by 21% and slashed pump energy use by 14% annually. Similarly, a semiconductor manufacturing facility in Singapore deployed 2-inch 3 way valves to manage etching fluids, increasing uptime by 16% over twelve months and cutting critical process interruptions to near-zero.
Smaller 1 4 inch models have seen wide acceptance in medical device fabrication and pharmaceutical manufacturing, where microbulk chemical blending is routine. Their rapid response time and non-reactive construction have contributed to batch quality improvements, with one case study showing a 9% reduction in QA rejections attributed to superior valve consistency. These examples highlight not only operational benefits but also the strategic ROI driven by investing in high-specification 3 way valve solutions.
Installation & Maintenance: Delivering Long-Term Performance
Proper installation and scheduled maintenance are essential to capitalize on the performance and reliability of 3 way valves. Installation should always ensure unidirectional or correctly oriented flow as per the manufacturer’s port diagram. For the 3 way valve 3 4 inch, hand-tightening followed by a calibrated torque wrench ensures leak-free seals without over-compressing gaskets.
Maintenance intervals primarily depend on cycle rates and the aggressiveness of media. For water or HVAC glycol, inspection every 18–24 months is typical. For corrosive chemicals, quarterly checks and annual replacement of elastomer seals are best practices. Automated valves fitted with position feedback offer predictive alerts, reducing unplanned downtime. Regular cleaning of ports using mild solvents, combined with prompt actuator recalibration, extends operational life and preserves peak flow rates.
Final Considerations: Selecting the Best 3 Way 3 4 Valve for System Optimization
Integrating the 3 way 3 4 valve or its related variants—whether in 2 inch or 1 4 inch sizes—into fluid control systems delivers measurable advantages in efficiency, adaptability, and maintenance. The decision process should weigh material compatibility, actuation needs, lifecycle costs, and regulatory requirements. Data-driven performance evaluation, as well as close collaboration with top manufacturers, ensures that every installation meets contemporary engineering standards and paves the way for next-generation automation.
By leveraging robust technical advancements, proven application successes, and tailored customization, selecting a 3 way 3 4 valve becomes a sustainable investment yielding lasting operational gains. As fluid dynamics and control system demands grow in complexity, these valves will remain central to innovative, future-proofed process management strategies.
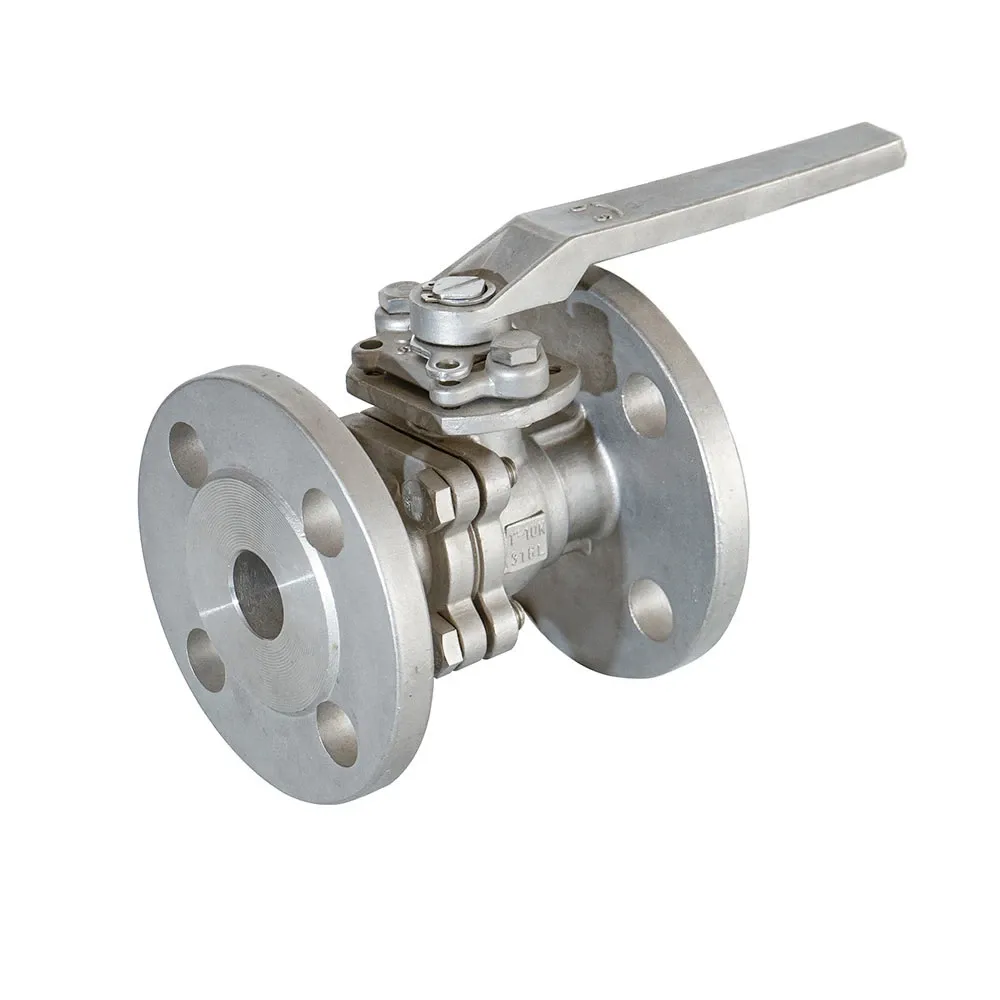
(3 way 3 4 valve)