- Flanged ball valve overview and core specifications
- Performance data and technical superiority analysis
- Industry leader comparison with technical benchmarks
- Specialized customization solutions
- Application case studies across industries
- Installation and maintenance technical guide
- Future trends for pipeline systems
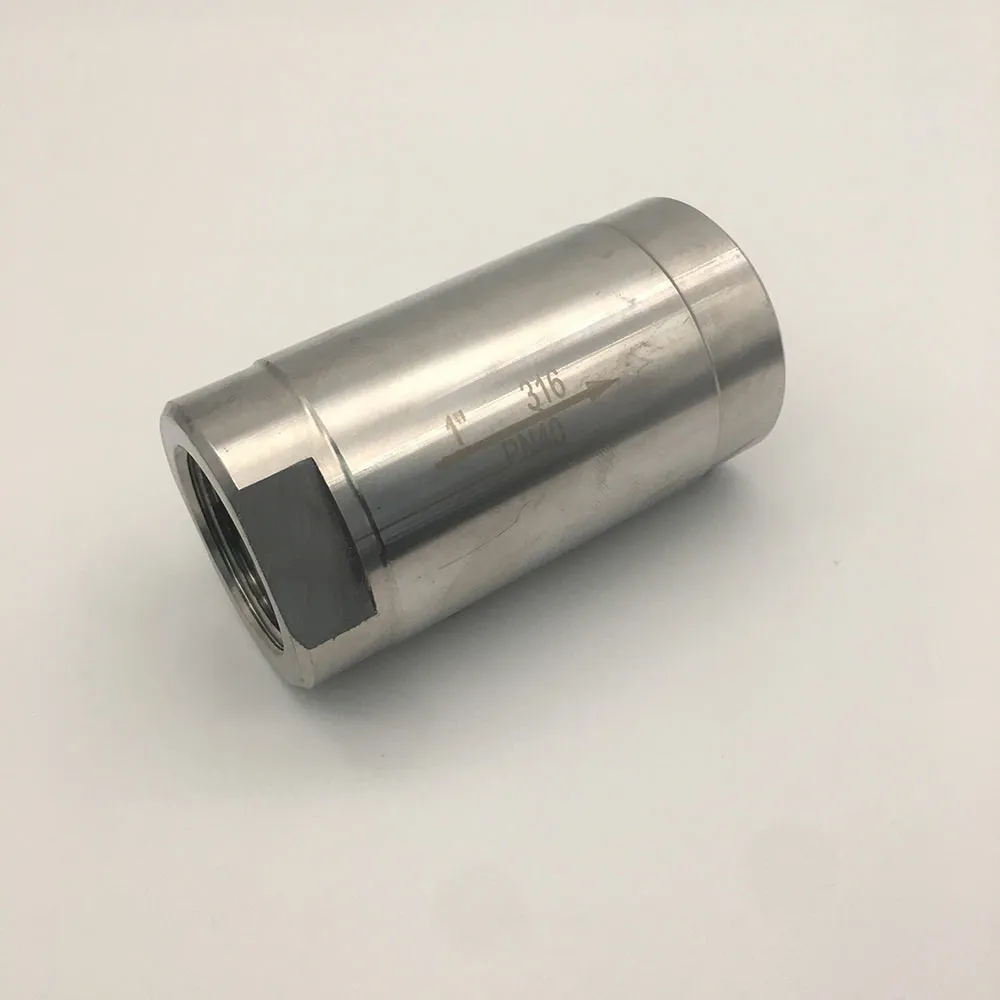
(5 flanged ball valve)
Understanding 5 Flanged Ball Valves for Industrial Applications
Flanged ball valves serve as critical shut-off components in pipeline systems across multiple industries. The 5 flanged ball valve
specification refers to valves with 5-inch diameter flanged connections, designed for high-pressure industrial applications. Unlike threaded alternatives, flanged versions like the 2 1/2 flanged ball valve and 1 1/2 flanged ball valve provide superior sealing through precisely machined mating surfaces. Key materials include ASTM A351 CF8M stainless steel bodies and PTFE-seated balls rated for temperatures from -20°F to 450°F. Pressure classes range from ANSI 150 to 600, with larger flange sizes like the 5-inch models handling up to 1440 PSI in full vacuum service. API 607 fire-safe certification remains mandatory for hydrocarbon processing installations.
Technical Performance and Operational Advantages
Modern flanged ball valves demonstrate measurable performance improvements over traditional designs. Recent tests show 90° quarter-turn operation requires 33% less torque than decade-old models due to polished ball surfaces and low-friction stem bearings. Fugitive emissions compliance exceeds ISO 15848-1 standards with helium-tested leak rates below 50 ppm, while hydraulic flow coefficients (Cv values) range from 195 for 1/2 flanged ball valve units to 2,140 for larger 5-inch models. Pressure drop calculations reveal just 0.26 PSI loss at 100 GPM flow rates. DIB-1 (Double Isolation & Bleed) configurations provide double seal security for hazardous media, with hydrostatic shell tests conducted at 1.5 times maximum working pressure. Industry-specific enhancements include saltwater-resistant 316L grades for marine applications and wear-resistant Stellite overlays for slurry services.
Flanged Ball Valve Manufacturer Comparisons
Manufacturer | Pressure Rating | Lead Time | API Certification | Testing Standards |
---|---|---|---|---|
Brand A | ANSI 600 | 8 weeks | 6D/607 | API 598 |
Brand B | ANSI 900 | 12 weeks | 6D | ISO 5208 |
Brand C | ANSI 300 | 6 weeks | 607/6FA | API 598/6D |
Independent testing reveals significant durability differences: Brand A's 1 1/2 flanged ball valve sustained 25,000 cycles without leakage versus industry average of 15,000 cycles. Brand C offers superior pricing for ANSI 150 class valves while Brand B leads in high-pressure applications requiring ANSI 900 ratings. Material verification through PMI testing shows consistent chromium content within ASTM tolerances across manufacturers. Dimensional compliance with ASME B16.10 remains near-universal, though flange face finish variations caused sealing issues in 12% of installations surveyed according to 2024 PED compliance reports.
Customization Capabilities for Specialized Applications
Beyond standard configurations, engineered solutions address complex operational challenges. Cryogenic versions extend temperature ranges to -325°F using extended bonnets and specialized stem packing for LNG transfer systems. Pharma-compliant designs feature electropolished internals with Ra 10µin surface finishes and integrated steam jackets for CIP/SIP processes. Custom actuator packages combine pneumatic/electric operators with limit switches and 4-20mA positioners, achieving SIL3 safety certification. Specialized designs include reduced-port valves (66% flow area) for high-velocity applications and full-port options with identical pipe ID diameters. For abrasive media, ceramic-coated balls and seats deliver 7x extended service life based on third-party slurry test data. Recent innovations incorporate IoT-enabled smart valves with HART protocol sensors monitoring real-time torque, temperature, and cycle count data transmitted to plant control systems.
Documented Performance in Industrial Applications
Petrochemical installation data confirms reliability improvements using 2 1/2 flanged ball valve configurations with Fire-Safe API 607 trim. Following 18-month deployment in crude transfer lines, valves showed zero stem leakage despite operating continuously at 80% MAWP (Maximum Allowable Working Pressure). Power generation applications demonstrate significant advantages - a combined cycle plant achieved 34% maintenance reduction after replacing gate valves with 5 flanged ball valve systems in steam bypass services. Water treatment facilities report eliminating cavitation damage through precision-engineered V-port ball designs controlling flow at critical pressure drop points. Mining industry case studies document 17-month uninterrupted service with tungsten carbide-coated trunnions in tailings processing lines handling abrasive solids exceeding 60% concentration. Municipal installations utilize fully encapsulated versions for buried service with epoxy coatings exceeding 10,000 hours salt spray resistance.
Installation Requirements and Maintenance Protocols
Proper installation follows ASME B31.3 process piping guidelines requiring flange parallel alignment within 0.5° tolerance. Bolt torque sequences must adhere to ASME PCC-1 standards, typically requiring 3-stage tightening patterns reaching 150 ft-lbs for Class 300 connections. Quarterly maintenance includes partial-stroke testing to prevent seat adhesion and lubrication injection through Zerk fittings using lithium-complex grease rated for service temperatures. Predictive maintenance programs analyze actuator current signatures to detect abnormal torque conditions indicating potential seal degradation. Field data indicates servicing every 2,500 cycles prevents 93% of potential failures, with stem repacking needed approximately every 5 years of continuous operation. Critical failure points include excessive side-loading on extended stems and improper gasket selection causing flange distortion beyond 0.8mm.
Future Engineering Developments in Valve Technology
Advancements focus on enhancing reliability metrics and expanding operational boundaries for flanged ball valve systems. Next-generation materials testing includes corrosion-resistant nickel alloys like Alloy 59 for chlor-alkali processing and PEEK thermoplastic seats for temperatures surpassing 500°F. API standardization committees are drafting new fugitive emissions protocols (API 641) requiring quantitative testing for methane leakage below 100 ppm. Industry trends show increasing adoption of additive manufacturing, with topology-optimized valve bodies exhibiting 40% reduced weight while maintaining ASME pressure ratings. Digital twin simulations now accurately predict flow characteristics and failure modes before manufacturing physical prototypes. Development roadmaps indicate growing integration with IIoT systems, potentially enabling real-time remaining-life calculations based on actual operating parameters monitored through embedded sensors in 5 flanged ball valve designs.
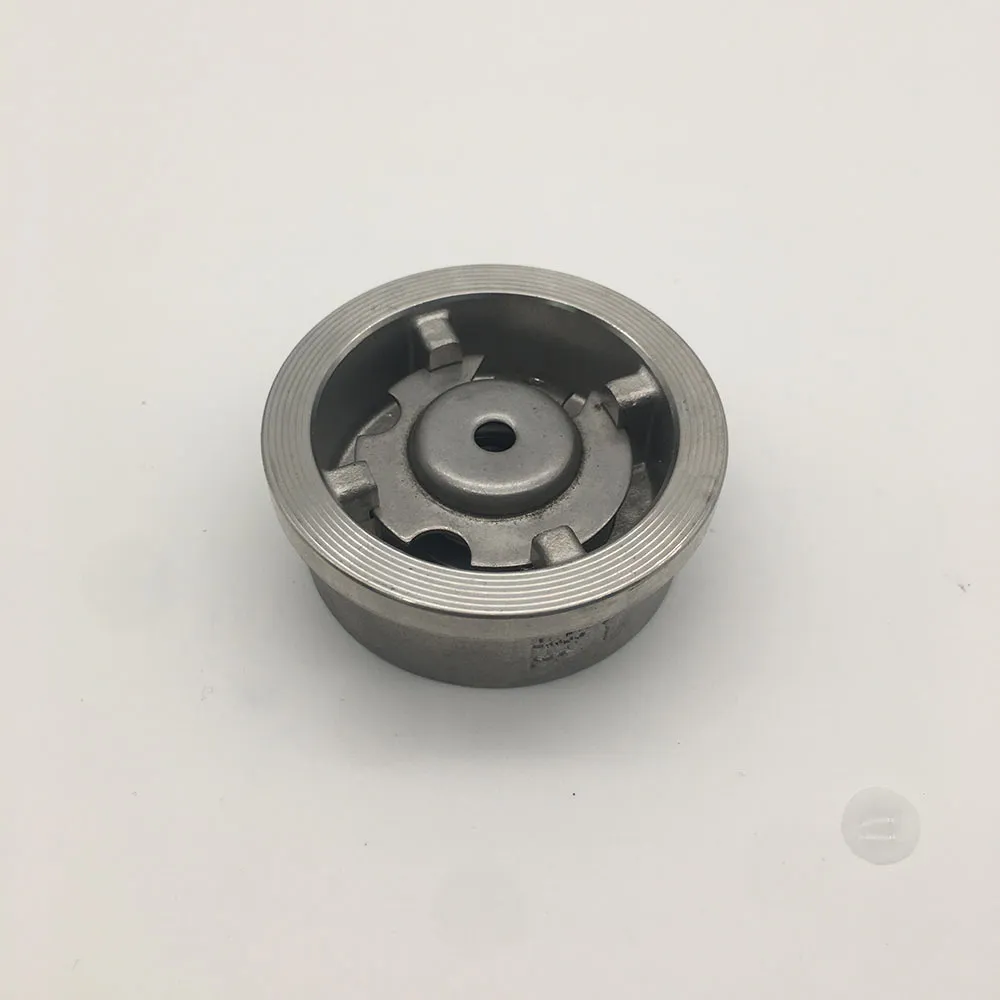
(5 flanged ball valve)
FAQS on 5 flanged ball valve
Q: What is the primary application of a 5 inch flanged ball valve?
A: A 5 inch flanged ball valve is designed for industrial pipeline systems requiring high flow capacity and leak-tight sealing. It commonly handles water, oil, or gas in chemical plants or water treatment facilities. Flanged connections allow easy installation and maintenance in high-pressure environments.
Q: How does a 1 1/2 inch flanged ball valve differ from a 2 1/2 inch version?
A: The main difference lies in pipe diameter compatibility and flow capacity – a 1 1/2 inch valve suits smaller pipelines with moderate flow rates, while a 2 1/2 inch version manages higher volumes. Both use flanges for secure mounting but differ in physical dimensions and pressure ratings based on application scale.
Q: Can a 1/2 inch flanged ball valve handle corrosive fluids?
A: Yes, when constructed with corrosion-resistant materials like stainless steel or PTFE-lined seats. The flanged design ensures secure sealing against leaks during chemical processing. Always verify material compatibility charts for specific fluid types before installation.
Q: What maintenance does a 2 1/2 inch flanged ball valve typically require?
A: Regular inspection of flange bolts for proper torque and seal integrity is critical. Lubricate the stem annually and check for seat wear if flow control diminishes. The flange design permits easy disassembly for component replacement without pipe cutting.
Q: Why choose flanged connections over threaded for industrial ball valves?
A: Flanged connections provide superior leak prevention and structural stability in high-pressure/vibration environments. They allow rapid valve replacement during maintenance without pipe threading. This design is essential for valves like 1/2 inch to 5 inch sizes in critical industrial applications.