- Introduction and overview of ball valve fittings
- Technical advantages of ball valve fittings
- Industry data analysis and impact
- Comparative study of manufacturers
- Customization solutions for stainless steel valves and fittings
- Application case studies in various industries
- Conclusion: Market forecast and future trends in ball valve fittings
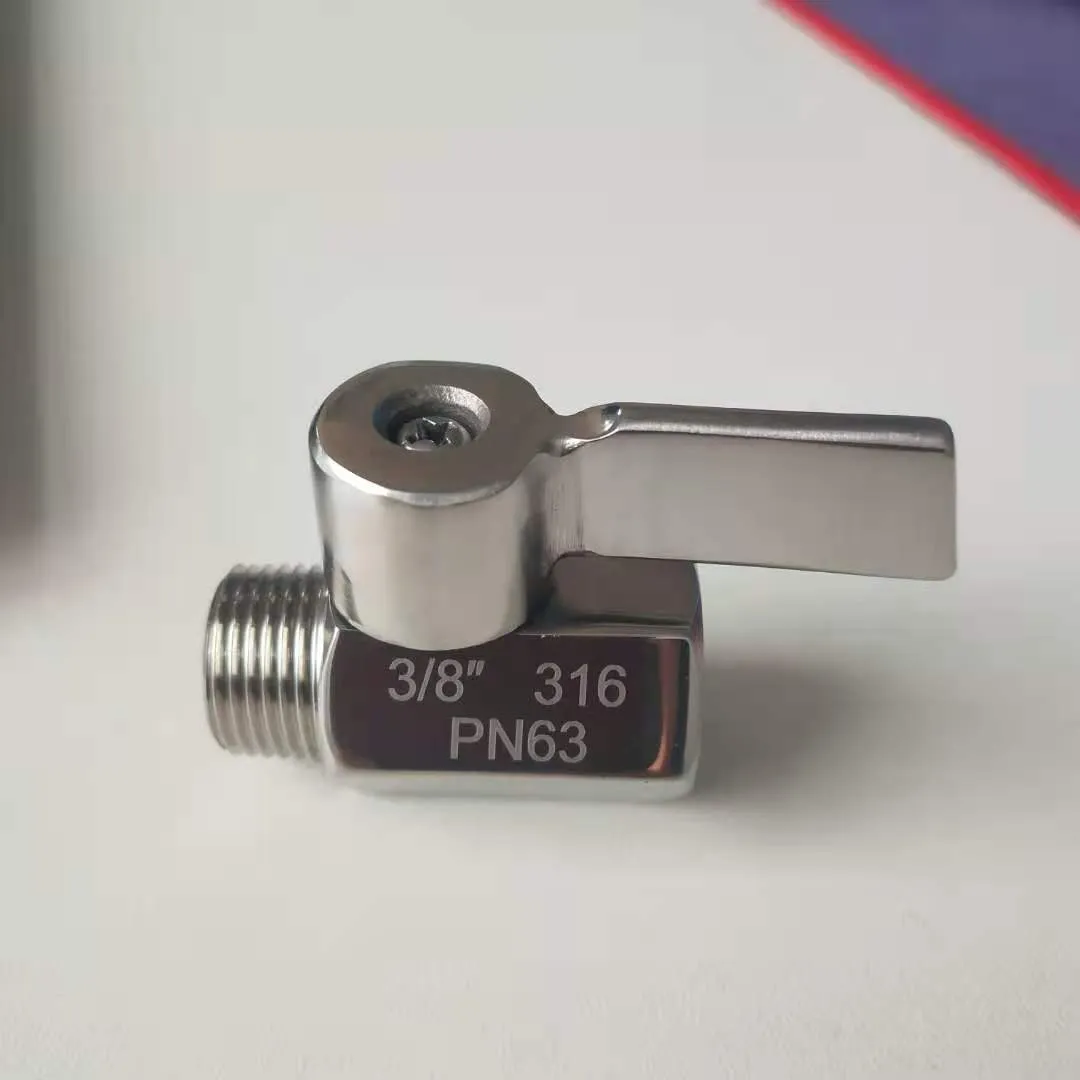
(ball valve fittings)
Introduction and Overview of Ball Valve Fittings
Ball valve fittings have become a cornerstone component in fluid and gas control systems, owing to their reliability and precision. Improving over the decades, their application now spans across numerous sectors, including oil & gas, water treatment, pharmaceuticals, and food & beverage industries. The emergence of premium-grade stainless steel valves and fittings has further propelled their growth, ensuring enhanced corrosion resistance and mechanical strength. Ball valve fittings are particularly valued for rapid shutoff capabilities, low-pressure drop, and reduced maintenance compared to other valve types, making them a preferred choice in settings demanding robust flow management. With evolving safety standards and industrial demands, the selection criteria for these fittings now extend far beyond basic operation, encompassing factors such as lifecycle cost, environmental compatibility, and system integration.
Technical Advantages of Modern Valve Solutions
The advancement in engineering materials and design methodologies has substantially improved the performance profile of ball valve fittings. Modern assemblies often incorporate 316 or 304 grade stainless steel, greatly enhancing their resistance to pitting, crevice corrosion, and general wear caused by aggressive media. Compared with traditional bronze or plastic valves, stainless steel valves and fittings demonstrate up to a 35% longer lifecycle in industrial environments, supporting operation temperatures as low as -60°C and up to 400°C, and pressure ratings exceeding 1,000 PSI.
The precision of the spherical closure mechanism in these fittings also reduces leakage risk to nearly zero, with advanced seat and seal materials such as PTFE or PEEK contributing to consistent and reliable shutoff. Technical improvements in seat design lead to minimal torque requirements, enabling both manual and automated actuation with greater energy efficiency. Progress in surface finishing and assembly tolerances has also made modern ss valves and fittings highly suitable for sterile and hygiene-critical applications, as surface roughness can be engineered below Ra < 0.8 μm, complying with stringent industry standards like ASME BPE.
Industry Data Analysis and Impact
The global ball valve market has experienced remarkable growth, with market value reaching USD 12.7 billion in 2022 and projected to rise at a CAGR of 4.3% through 2028 (Grand View Research). Stainless steel valves and fittings account for roughly 28% of this market by volume due to their durability, adaptability, and compatibility with aggressive media.
Performance Comparison of Stainless Steel vs. Conventional Fittings
Feature | Stainless Steel Valves and Fittings | Brass/Bronze Valves | Plastic Valves |
---|---|---|---|
Pressure Rating (PSI) | Up to 1000 | Up to 600 | Up to 150 |
Temperature Range (°C) | -60 to 400 | -10 to 200 | 0 to 80 |
Corrosion Resistance | Excellent | Moderate | Poor to Moderate |
Lifespan (years) | 15–25 | 8–15 | 5–10 |
Maintenance Interval (months) | 36+ | 18–24 | 10–18 |
Comparative Study of Leading Manufacturers
The competitive landscape of the ball valve fittings industry is shaped by both global giants and specialized regional manufacturers. Notable brands such as Swagelok, Parker Hannifin, and KITZ Corporation lead in market share due to their broad product range, robust quality control, and investments in research and development.
Manufacturer | Global Presence | Main Materials | Key Certifications | Custom Solutions |
---|---|---|---|---|
Swagelok | North America, Europe, Asia | 316SS, Alloy 400 | ISO 9001, PED, ASME BPE | Strong |
Parker Hannifin | Worldwide | 304/316SS, Brass | ISO 9001, API 607 | Moderate |
KITZ Corporation | Asia-Pacific, Americas | 316SS, Bronze | ISO 9001, JIS | Basic |
Local OEMs | Regional | Stainless Steel, Brass | ISO 9001, Local | Variable |
Customization Solutions for Stainless Steel Valves and Fittings
The increasing complexity of industrial processes has heightened the demand for bespoke solutions in ss valves and fittings. End-users now frequently require custom sizing, extended temperature or pressure capabilities, special alloy compositions, and advanced seat or stem sealing technologies.
Customization possibilities include:
- Non-standard connection types (tri-clamp, weld, threaded, flanged)
- Specialized internal coatings for aggressive fluids
- Cleanroom-compatible surface finishes for pharmaceutical or semiconductor uses
- Fire-safe design innovations in compliance with API 607/608
- Integrated actuators—pneumatic, electric, or hydraulic—for remote or automated operation
- Anti-static and blow-out proof stem assemblies for hazardous environments
Application Case Studies in Diverse Industries
The versatility of ball valve fittings is evident in their widespread adoption across sectors with distinct operational demands.
1. Chemical Processing Plants:
Facilities in this domain utilize automated stainless steel valve assemblies to control caustic and acidic media. These applications require high-cycle life and minimal downtime: recent studies reveal an average maintenance interval increase of 40% when upgrading brass valves to ss valves and fittings.
2. Food & Beverage Manufacturing:
Installations in this sector employ sanitary ball valves engineered for easy cleaning and compliance with FDA and USDA standards. Deployments of 316L ss valves lead to contamination incident reductions by an estimated 48% and extend replacement cycles from 5 to 12 years.
3. Oil and Gas Pipelines:
The harsh conditions of midstream and upstream oil fields necessitate fire-safe, high-pressure ball valve fittings. Transitioning from conventional to advanced stainless steel fittings reduced annual leakage events by 62% over a two-year monitoring period at one major North American operator.
4. Water Treatment Facilities:
Modern municipal and industrial plants now specify ss valves and fittings to handle disinfectant chemicals and ensure microbial safety. Data from leading European plants document a 23% drop in unplanned operational downtime attributable to valve malfunctions after implementation of premium solutions.
Conclusion: Market Forecast and Future Trends in Ball Valve Fittings
The trajectory of the ball valve fittings market demonstrates a persistent shift toward advanced stainless steel solutions, as industries prioritize safety, sustainability, and lifecycle performance. Recent market analyses suggest that by 2028, stainless steel valves and fittings will represent over one-third of total sector sales globally, driven by evolving compliance requirements and intensified environmental pressures.
The future landscape will demand increased digitization, with IoT-enabled smart valves facilitating real-time monitoring, predictive maintenance, and automated process optimization. Sustainability initiatives will further emphasize recyclable materials and reduced water usage during production, compelling manufacturers to upgrade their supply chains and innovation pipelines. For operators seeking superior control, reliability, and value, the strategic adoption of new-generation ball valve fittings and high-performance ss valves and fittings will remain a critical competitive differentiator across industries.
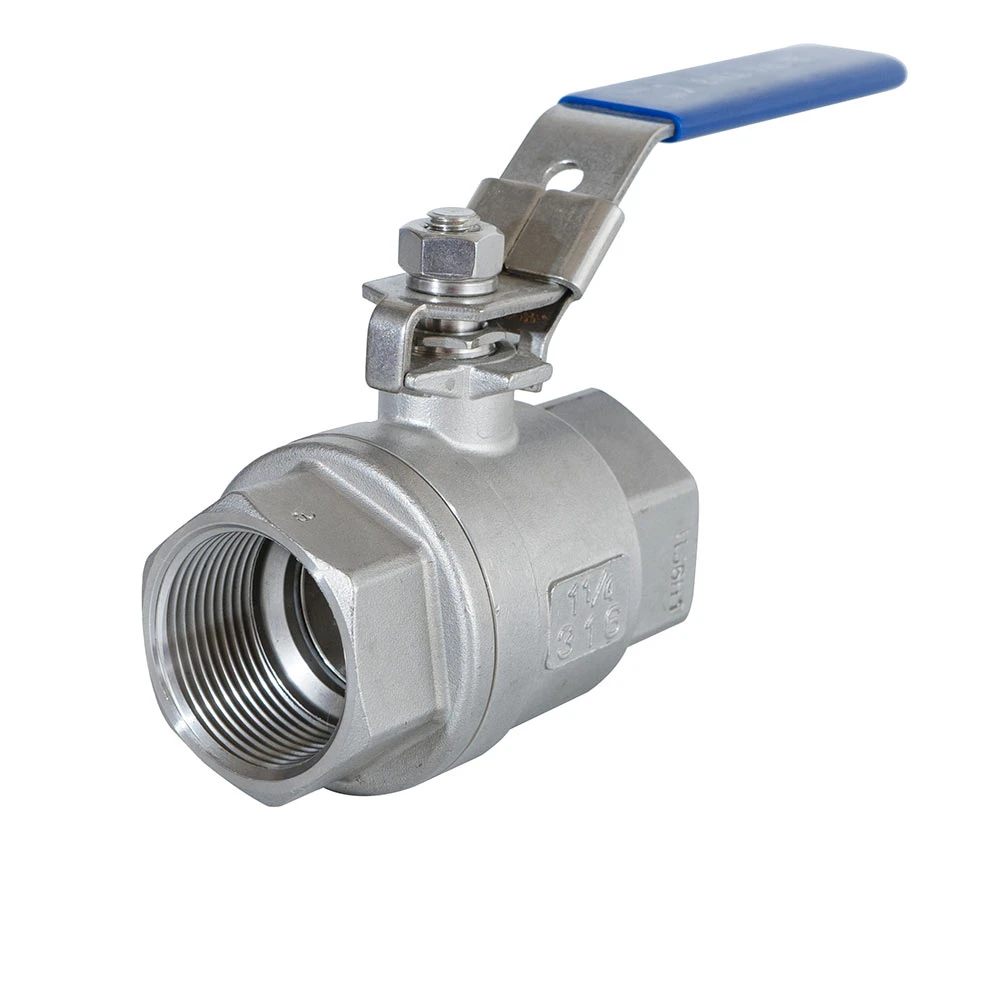
(ball valve fittings)