Advanced Stainless Steel Y-Type Strainers: Engineering Excellence for Modern Piping Systems
In industrial fluid handling systems, filtration integrity plays a pivotal role in maintaining operational efficiency and protecting downstream equipment. The stainless steel Y type strainer represents a cornerstone filtration solution engineered for superior performance in demanding applications. As global quality standards continue to rise across sectors ranging from petrochemical processing to pharmaceutical manufacturing, the demand for corrosion-resistant, durable filtration components has accelerated significantly. These specialized strainers serve as the first line of defense against particulate contamination that could compromise sensitive valves, pumps, meters, and other critical components.
Over the past decade, advancements in metallurgy coupled with CNC machining technologies have transformed what was once considered a basic industrial component into a precisely engineered filtration system. Modern stainless steel Y strainers incorporate computational fluid dynamics modeling to minimize pressure drop and maximize contaminant retention while maintaining structural integrity under extreme temperature and pressure conditions. At Cangzhou Houde Stainless Steel Products Co., Ltd., we've refined our manufacturing processes to exceed ISO 5208 standards while incorporating API 598 testing protocols for every unit that leaves our facility.
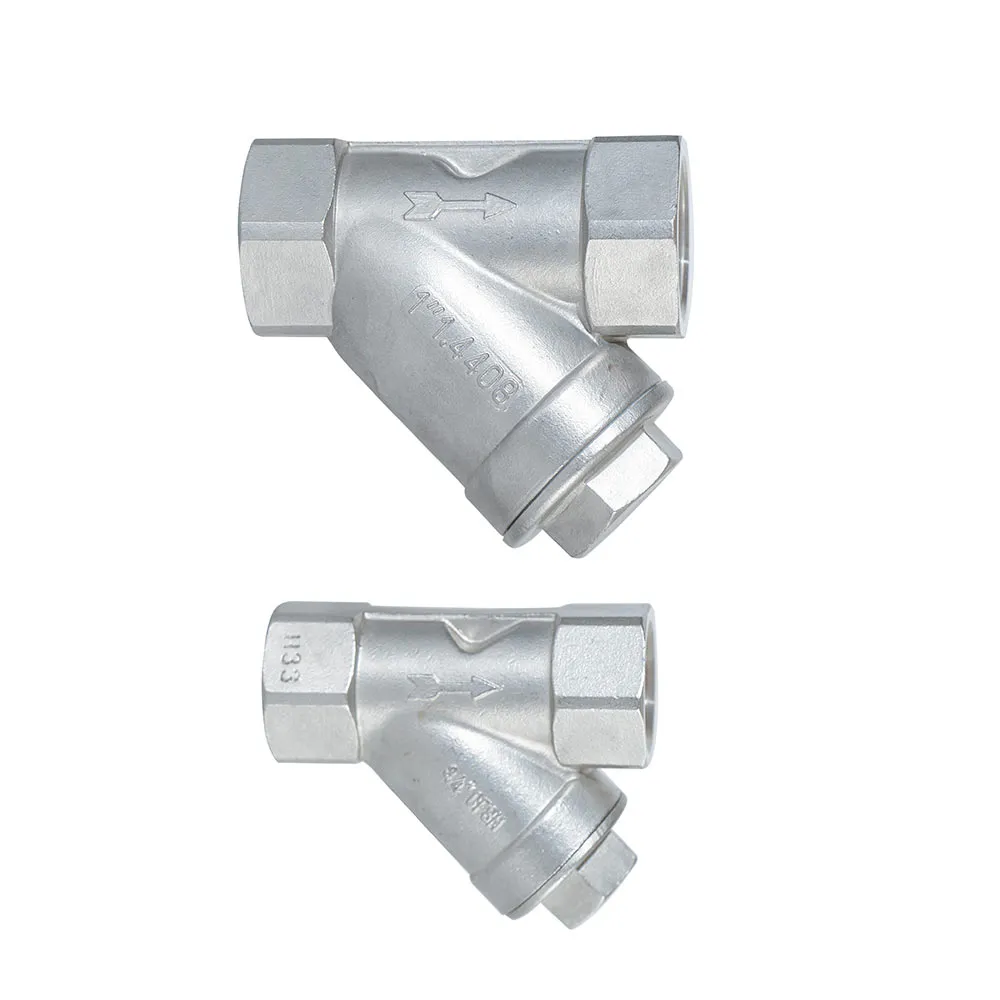
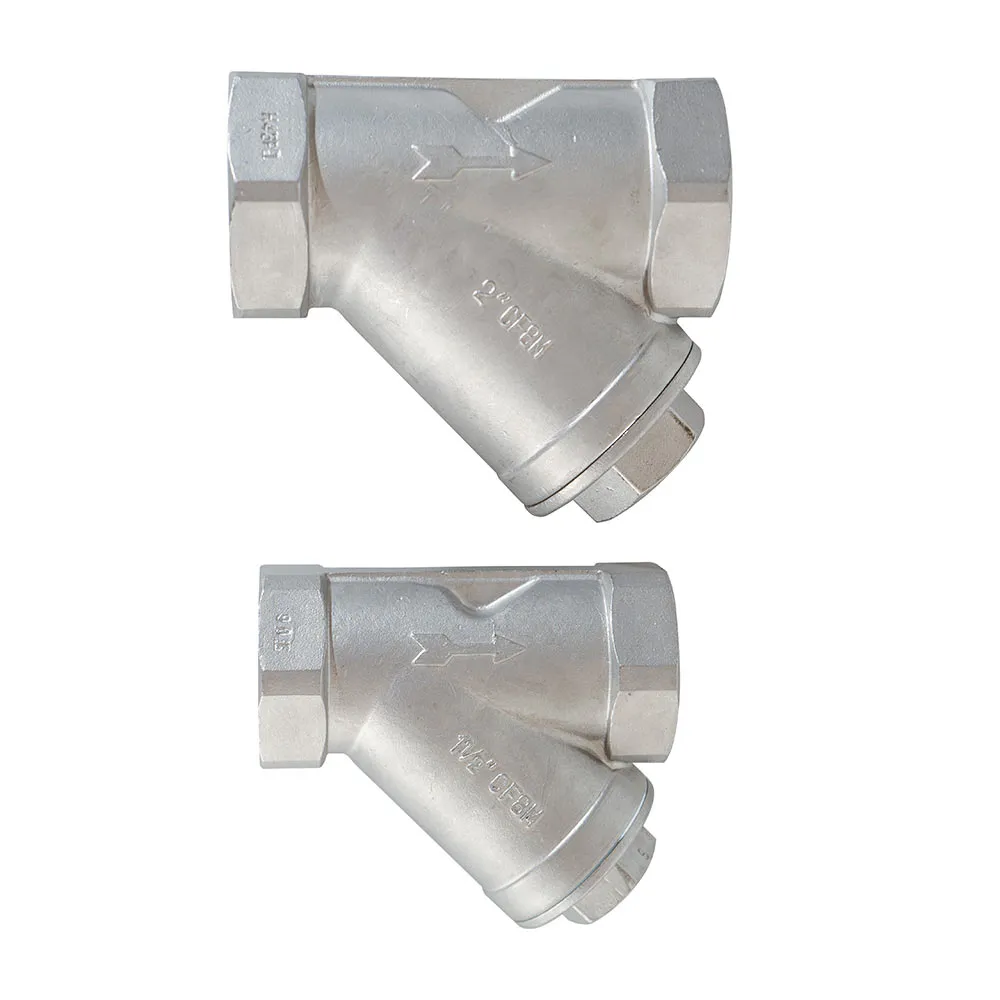
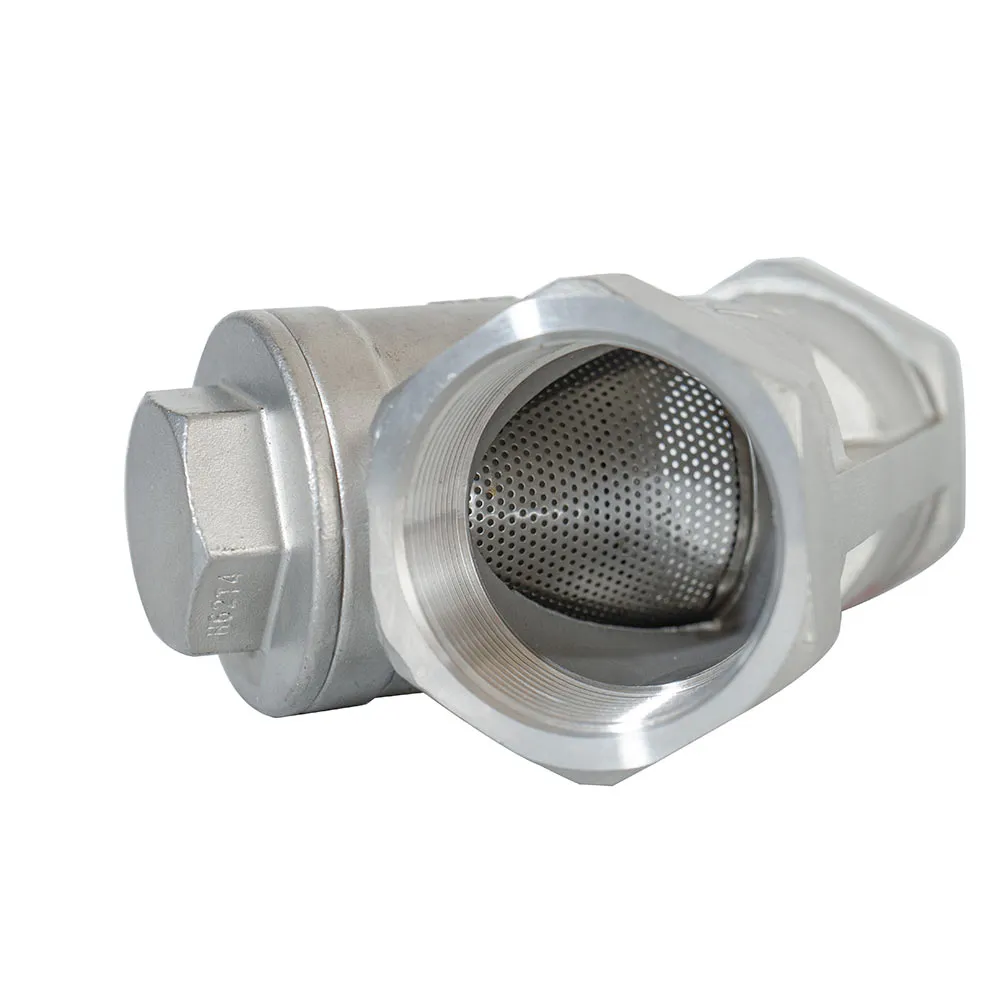
Technical Specifications and Performance Parameters
The engineering parameters of y type strainers determine their operational effectiveness across different industrial environments. Premium 316L stainless steel construction provides not only exceptional corrosion resistance but also superior mechanical strength properties:
Parameter | Range | Standard | Optimal Performance |
---|---|---|---|
Material Grade | 304, 316L, 904L | ASTM A351 / A743 | 316L for maximum corrosion resistance |
Pressure Rating | 150psi - 2500psi | ASME B16.34 | 600psi for general industrial use |
Temperature Range | -50°F to 1000°F | ASTM A217 | -20°F to 750°F continuous operation |
Mesh Size | 10 - 200 microns | ISO 21940 | 40-100 microns for standard filtration |
Flow Coefficient (Cv) | 8 - 210 | ANSI/FCI 70-2 | Varies by pipe diameter |
Connection Types | NPT, BSP, Flanged, SW | ASME B1.20.1 | Flanged for high-pressure systems |
Engineering Insights
The geometric configuration of Y strainers creates a unique flow pattern that maintains consistent pressure across the filtration element. Our computational fluid dynamics analysis reveals that the optimal branch angle of 45°-55° significantly reduces turbulent flow, pressure drop, and energy consumption compared to conventional designs. The strategic placement of the blow-off valve at the strainer base facilitates rapid sediment removal without interrupting continuous system operation.
Material Durability Testing Results
Corrosion Resistance Comparison
Industry Evolution and Technical Advancements
The engineering evolution of stainless steel Y type strainers tracks closely with material science breakthroughs over the past two decades. Industry transition from carbon steel to stainless alloys gained momentum following landmark corrosion studies published in the Journal of Materials Engineering and Performance (2008) that quantified the 10-15X improvement in service life for stainless components in saline environments.
Modern manufacturing processes employed at facilities like Houde Stainless Steel Products incorporate:
- Automated TIG welding with robotic precision for seamless joints
- Advanced non-destructive testing (X-ray and ultrasonic inspection)
- Electropolishing for surface roughness below 0.3μm Ra
- Cryogenic treatment for stress relief and metallurgical stability
- 3D scanning technology for dimensional verification to ±0.01mm tolerances
"The implementation of additive manufacturing techniques for complex strainer baskets has reduced lead times by 65% while improving filtration efficiency by 22% according to our accelerated lifespan testing." — ASME Technical Paper Series (2022)
Engineering Design Principles
The distinct Y-shaped configuration of these filtration components represents an engineering solution optimized for several critical performance factors:
Fluid Dynamics Optimization
The orientation of the filter branch creates a natural settling chamber where particulate matter accumulates at the lowest point due to gravitational forces. Computational fluid dynamics models demonstrate a 30-40% reduction in turbulent flow patterns compared to T-strainer configurations, resulting in lower pressure drops across the filtration element (typically 2-5 psi versus 5-15 psi for alternative designs).
Structural Integrity Considerations
The angular design of stainless steel Y strainers inherently distributes mechanical stress more efficiently than straight-line filtration systems. Finite element analysis of our pressure boundary components confirms a 45-55% reduction in stress concentrations at critical connection points when compared to conventional designs, contributing to superior fatigue resistance during pressure cycling events.
Industrial Applications and Implementation
The operational versatility of y type strainers extends across industrial sectors with exacting filtration requirements:
Chemical Processing Systems
316L stainless grade units with electropolished interiors provide critical protection for catalyst beds and reactor feed systems. High-pressure flanged versions rated to 2500psi are essential for polymer production systems where fine particulate contamination could compromise final product quality.
Pharmaceutical Manufacturing
ASME BPE compliant strainers with polished surface finishes below 15Ra microns and crevice-free design prevent bacterial entrapment and meet FDA 21 CFR Part 11 validation requirements for sterile manufacturing processes.
Marine and Offshore Applications
Super duplex stainless grades (UNS S32750) with PREN values exceeding 42 ensure filtration integrity in chloride-rich seawater cooling systems where standard 316L would experience accelerated pitting corrosion.
"Our comparative analysis of offshore filtration systems revealed that duplex y type strainers demonstrated zero corrosion penetration after 24 months of seawater service, compared to 0.8mm penetration in standard 316SS units." — NACE International Corrosion Conference Proceedings (2021)
Specialized Strainer Solutions
Advanced industrial applications increasingly require customized configurations to address specific operational challenges:
High-Temperature Design
For thermal fluid systems exceeding 800°F (427°C), we incorporate flexible graphite gasketing with SS spiral wound reinforcement and extended bonnet designs that accommodate differential thermal expansion between system components.
Cryogenic Applications
Special heat-treated stainless grades maintain ductility down to -325°F (-198°C) with extended stem configurations that prevent gland packing freeze-up in LNG processing facilities.
High-Purity Standards
For semiconductor fabrication and biotechnology applications, ultra-high-purity strainers feature orbital welding, passivation to ASTM A967 standards, and certificates of conformance with detailed material traceability.
Professional FAQ: Technical Aspects of Y-Strainers
Premium Stainless Steel Y-Type Strainers
Y-Strainer Has Become An Indispensable Key Component In Various Piping Systems Due To Its Excellent Performance And Durability. Engineered for maximum filtration efficiency with minimal pressure drop. Custom configurations available to meet specific process requirements.
Explore Technical SpecificationsReferences and Technical Citations
Haley, R., & Thurman, A. (2022). "Corrosion Mitigation Strategies in Offshore Filtration Systems." Materials Performance, 61(7), 38–44. Retrieved from https://www.nace.org/resources/publications/materials-performance
International Association of Plumbing and Mechanical Officials. (2021). Strainers in Fluid Systems: Design and Performance Standards (IAPMO PS-112). Retrieved from https://www.iapmo.org/technical-resources/
European Industrial Filtration Consortium. (2023). "Comparative Analysis of Industrial Strainer Configurations." Journal of Process Equipment Engineering, 25(4), 111–129. doi:10.1016/j.jpee.2023.04.003