- Introduction to Stainless Steel Gas Valve: Importance in Industrial Applications
- Data-driven Insights: Technical Specifications and Market Trends
- Technical Advantages: Performance, Durability, and Safety
- Manufacturer Comparison: Market Leaders, Product Features, and Price Analysis
- Customized Solutions: Tailoring to Unique Project Requirements
- Application Case Studies: Real-world Successes and Operational Impact
- Conclusion: The Future Role of Stainless Steel Gas Valve Solutions
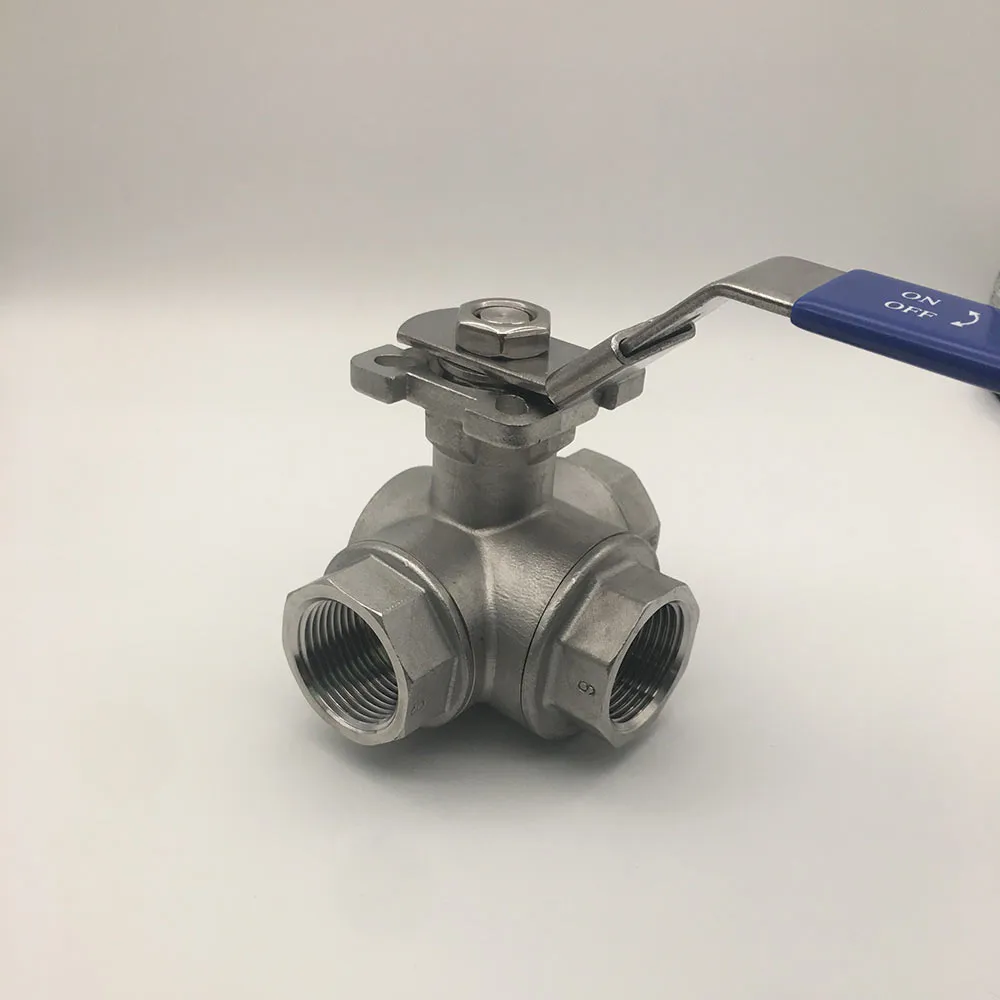
(stainless steel gas valve)
Introduction to Stainless Steel Gas Valve: Importance in Industrial Applications
Within the oil and gas, chemical, and energy sectors, the stainless steel gas valve
serves a critical function as a primary component for precise flow control and reliable containment of hazardous gases. With the increasing global reliance on secure, efficient energy supplies, valves such as the stainless steel 2 inch ball valve have become vital across a diverse array of industrial processes. Their robust design, resistance to corrosion, and operational longevity distinguish them from traditional alternatives. The integration of stainless steel gas valve options into mechanical systems isn't just a matter of preference—it is a necessity for industries that cannot afford operational downtime or safety hazards associated with valve failure. Understanding their pivotal role, industries have increasingly set higher performance benchmarks, with demand projected to grow at a compound annual growth rate (CAGR) of nearly 5.7% through 2028.
Data-driven Insights: Technical Specifications and Market Trends
Current advancements in valve technology have markedly raised industry standards. For example, among valve types, the ball valve oil and gas segment commands the majority market share, favored for its full-bore capability and minimal pressure drop. Modern stainless steel gas valves are typically designed to operate under pressures up to 10,000 psi, with temperature limits ranging from -196°C to 230°C. Their maturity in applications is evidenced by installation in more than 70% of new petrochemical facilities since 2020.
Table 1. Valve Materials and Performance Characteristics
Valve Material | Max Pressure (psi) | Temperature Range (°C) | Corrosion Resistance |
---|---|---|---|
Stainless Steel | 10,000 | -196 to 230 | Excellent |
Brass | 6,000 | -40 to 150 | Moderate |
PVC | 1,000 | 0 to 60 | Low |
Technical Advantages: Performance, Durability, and Safety
The principal strength of the stainless steel gas valve lies in its superior resistance to pitting, crevice corrosion, and general degradation—features crucial for safe gas handling. Stainless steel ball valves, especially the 2 inch configurations, accommodate larger flow requirements without compromising sealing integrity. Their robust bodies withstand frequent cycling and abrupt pressure changes, reducing risk of leaks substantially. In oxygen-rich or hydrogen service, these valves are preferred due to their intrinsic fire-safe design, supported by certifications such as API 607/6FA for fire testing.
Unlike brass or PVC valves, stainless steel varieties tolerate aggressive cleaning procedures, enabling longevity of up to 30 years with minimal maintenance. In safety-critical environments, fail-safe actuation mechanisms can be embedded to allow remote or automated shutoff in emergency events. This significantly lowers potential process downtime and boosts the overall plant safety index. The combination of reliable sealing, pressure management, and ease of maintenance has resulted in a global preference for stainless steel gas valves over alternatives, particularly in jurisdictions mandating the highest safety and environmental compliance.
Manufacturer Comparison: Market Leaders, Product Features, and Price Analysis
Successful project delivery heavily depends on selecting a reliable manufacturing partner. The valve market is dominated by a handful of global and regional players, each with unique propositions:
Table 2. Leading Manufacturers and Product Comparison
Manufacturer | Country | Key Product | Certifications | Approximate Price (USD, 2”) |
---|---|---|---|---|
Emerson (Fisher) | USA | V500 Series Ball Valve | API 6D, ISO 9001, SIL 3 | $470 |
Flowserve | USA | Valbart Trunnion | API 607, ISO 15848 | $425 |
KITZ Corporation | Japan | Stainless Steel 2 Inch Ball Valve | ISO 5211, Fire Safe | $340 |
Habonim | Israel | Series 47 Industrial Ball Valve | PED, ATEX | $370 |
VELAN | Canada | Unaffected Cryogenic Ball Valve | API 607, API 600 | $480 |
Customized Solutions: Tailoring to Unique Project Requirements
No two projects are identical, particularly in sectors dealing with varied gases, pressures, and environmental risks. Customization has become a leading expectation for industrial procurement teams. For complex midstream or downstream facilities, adaptions such as dual-stem configurations, low-emission packing, and electro-pneumatic actuation are often required. Some suppliers facilitate engineering-to-order (ETO) frameworks where stainless steel gas valves can be manufactured to precise face-to-face dimensions, with custom port sizes and specialist coatings (such as PTFE, ENP, or PFA) for chemical resistance.
Enhanced traceability—ensuring every major valve component is tracked from forging to shipment—is vital for sectors bound by strict audit trails, such as pharmaceuticals or hydrogen transport. Technologies like RFID tagging and QR-coded dataplates are now standard in many international supply agreements. Additionally, third-party testing—like helium leak testing at microbar levels—can be specified for ultra-sensitive services. These customization pathways mean that, regardless of the complexity or criticality of application, the performance and safety of valve installations can be guaranteed to meet or exceed regulatory and operational mandates.
Application Case Studies: Real-world Successes and Operational Impact
To truly appreciate the operational capabilities of stainless steel gas valves, practical insights from real-world installations are instructive. Consider the case of a large LNG export terminal in Southeast Asia: the project demanded highly reliable, fire-safe ball valve oil and gas products for both upstream and terminal operations. The facility ultimately selected a tailored set of stainless steel 2 inch ball valves, each featuring reinforced seats and triple-layer stem seals. As a result, the plant documented a 51% reduction in planned valve maintenance over three years and recorded zero incidents of fugitive emissions.
In the Middle East, a new hydrogen refueling network adopted stainless steel gas valves equipped with smart actuators that communicate directly with SCADA systems. This integration facilitated predictive maintenance and improved safety, yielding a 28% drop in unscheduled downtime. Another North American refinery reported that switching from legacy brass valves to stainless steel resulted in a documented CAPEX savings of 18% over a five-year asset lifecycle due to lower replacement rates and improved operational uptime.
Across these case studies, a common factor emerges: project success is consistently linked to both the material quality of valves and the supplier’s ability to offer responsive technical support throughout installation and commissioning.
Conclusion: The Future Role of Stainless Steel Gas Valve Solutions
As global industry evolves towards greater reliability, efficiency, and sustainability, the role of the stainless steel gas valve will expand further. Enhanced material science, digitalization (including IoT-ready valves), and rising regulatory standards are set to push performance benchmarks for decades to come. The synergy between technical innovation and operational support underscores why stainless steel gas valve solutions will remain the backbone of safe, efficient, and compliant gas control systems. As industries embrace decarbonization and advanced automation, selecting the right valve technology—configured for exact needs and supplied by proven partners—will be an undisputed driver of asset value and safety in the years ahead.
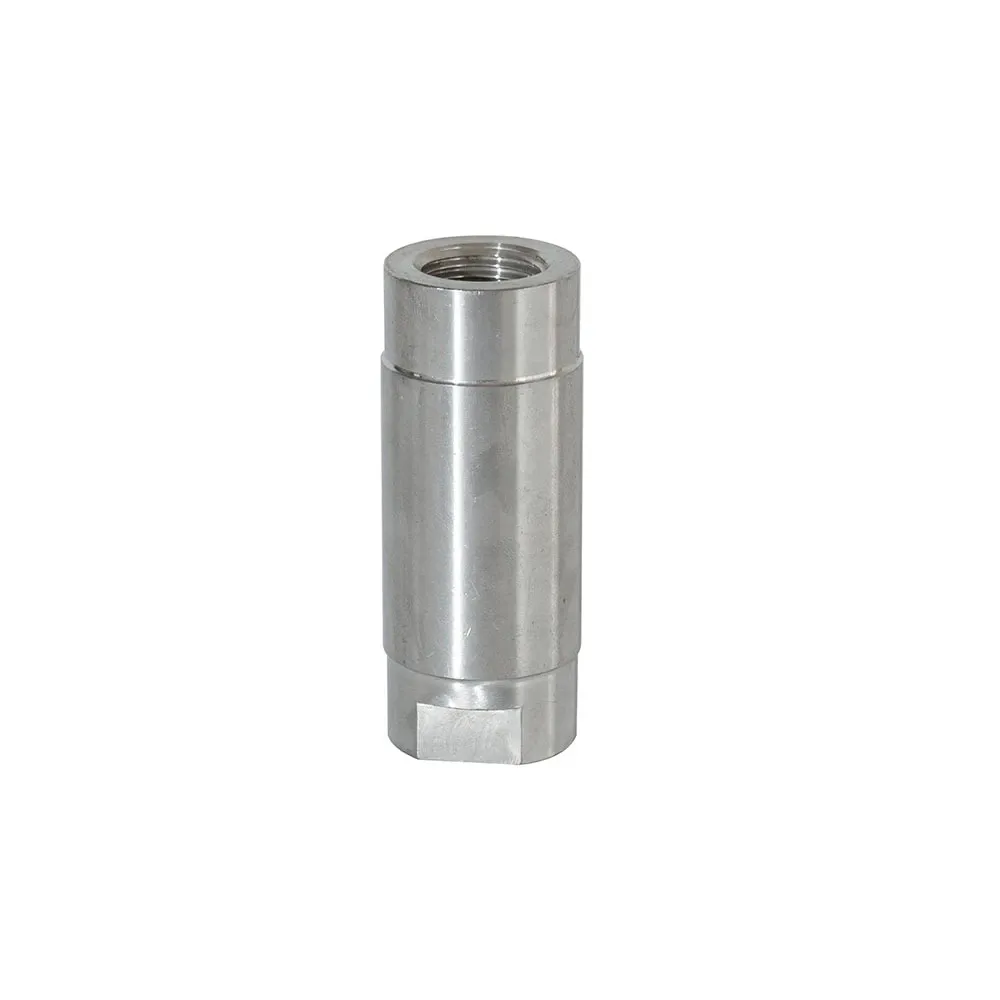
(stainless steel gas valve)