- Introduction to strainer types in piping
- Common functional categories of strainer designs
- Data comparison: performance and cost analysis of pipe strainer types
- Technical benefits and industry innovations
- Market manufacturers: benchmarking and differentiation
- Custom engineering solutions and selection criteria
- Application scenarios and case studies for types of strainer in piping
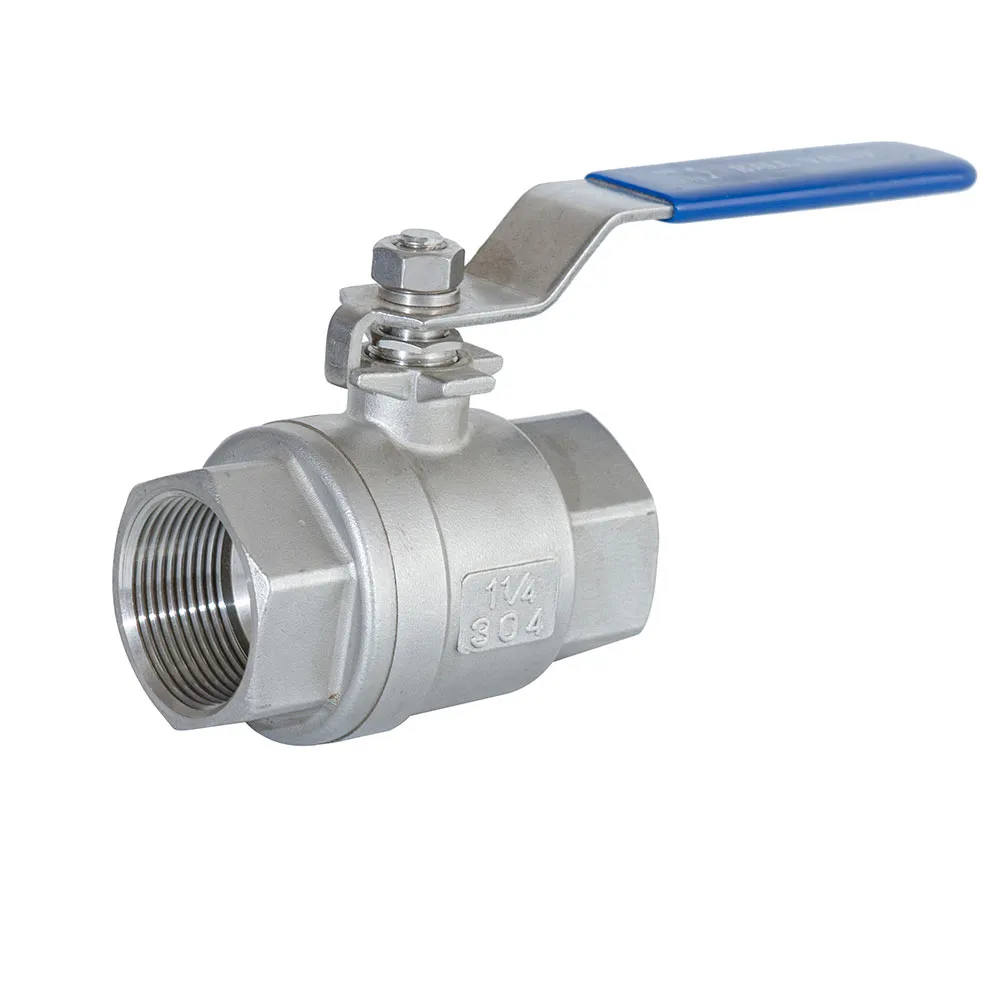
(strainer types in piping)
Introduction to Strainer Types in Piping Systems
Strainers are vital components in piping networks across diverse industries, responsible for mechanically removing debris and foreign particles to protect sensitive equipment, improve process efficiency, and minimize maintenance demands. Understanding strainer types in piping, along with their unique operational features, is fundamental when engineering cost-effective and reliable flow systems. The careful selection and implementation of the correct strainer type is a calculated process that balances the filtration requirement, installation constraints, service environment, and total cost of ownership. This overview outlines the primary categories, performance attributes, technical advantages, and provides a comparative analysis to aid informed decisions for any pipeline project.
Functional Categories of Pipe Strainer Types
Pipe strainer types generally fall into three predominant categories: Y-strainers, basket (or T-type) strainers, and duplex strainers. Each design adheres to specific use cases:
- Y-strainers: Characterized by their compact Y-shaped body, these strainers are ideal for small debris removal, suitable for vertical and horizontal installations, and often deployed in steam, liquid, or gas lines where periodic cleaning is acceptable.
- Basket strainers: Featuring a larger filtration area, basket strainers are well-suited for applications with higher dirt loading, ensuring extended service intervals. They are predominantly used on liquid systems, where low-pressure drop is essential.
- Duplex strainers: Engineered for continuous operations, duplex strainer setups allow for uninterrupted filtration by switching flow between two parallel baskets during maintenance, making them the preferred choice in critical processes.
Performance and Cost Analysis: Strainer Types in Practice
For engineers and procurement managers, evaluating types of strainer in piping involves an examination of metrics like filtration efficiency (micron rating), pressure drop, maintenance workload, and budget impact. The following table compares the primary pipe strainer types on critical parameters:
Strainer Type | Typical Applications | Micron Rating Range | Pressure Drop (Clean) | Maintenance Frequency | Average Initial Cost | Operational Downtime (for cleaning) |
---|---|---|---|---|---|---|
Y-Strainer | Steam, air, low-viscosity liquids | 40–800 μm | Low to Moderate | Periodical manual cleaning | $$ | Required |
Basket Strainer | Water, fuel, lubricants, chemicals | 20–3,000 μm | Low | Less frequent, higher debris capacity | $$$ | Required |
Duplex Strainer | Continuous process, oil & gas, chemical plants | 20–1,500 μm | Low | On-the-fly basket changeover | $$$$ | Uninterrupted |
Self-cleaning Strainer | Raw water, process water, abrasive fluids | 10–500 μm | Variable | Automated, minimal manual intervention | $$$$$ | Negligible |
For instance, basket strainers can remove up to 80–90% of contaminants at typical micron ratings, while self-cleaning models drastically reduce labor and increase uptime in large cooling or industrial water systems. The initial investment is higher for automated solutions, but operational expenditure and process safety gains often justify the cost in high-throughput environments.
Technical Benefits and Ongoing Innovations
Advancements in strainer design in recent years have focused on filtration adaptability, simplified maintenance, and sustainability. Modern pipe strainer types benefit from robust corrosion-resistant alloys, engineered mesh and wedge wire elements, quick-release covers, and real-time fouling indicators. These improvements result in substantial reductions in lifecycle costs and downtime. In high-pressure and corrosive environments, stainless steel and specialty alloys have demonstrated up to 40% longer operational lifespans, while high-efficiency element geometries can decrease pressure drops by 30% compared to legacy models.
Manufacturers are also integrating digital monitoring and automatic backflush mechanisms, responding to Industry 4.0 requirements. Such advancements enable predictive maintenance strategies and real-time data acquisition, vital for critical infrastructures in pharmaceuticals, power generation, and food processing industries.
Manufacturer Comparison and Industry Benchmarks
Selecting a strainer goes beyond design; manufacturer expertise and after-sales support are critical considerations. Leading global players in the field—such as Eaton, Spirax Sarco, Hayward, and Armstrong—offer comprehensive portfolios that serve overlapping but unique industries. Below is a comparative analysis of top brands:
Manufacturer | Key Strainer Lines | Material Range | Certifications | Global Support | Custom Engineering |
---|---|---|---|---|---|
Eaton | Y, basket, duplex, automatic | Bronze, cast steel, SS, exotic alloys | ASME, ISO, UL | Worldwide | ✔ |
Spirax Sarco | Y, basket, T-strainers | Cast iron, SS, carbon steel | ASME, PED | Global | ✔ |
Hayward | Basket, Y, duplex | Thermoplastics, SS, iron | FDA, NSF, ISO | North America, EMEA | Partial |
Armstrong | Y, basket | Iron, bronze, SS | ASME, ISO | Americas, APAC | ✔ |
While all offer robust warranties and product innovation, differences emerge in their customization capabilities, material variety, and regional presence. For high-spec projects—such as offshore oil extraction—partnership with manufacturers offering deep application support and advanced material science expertise is a critical comparative advantage.
Custom Engineering: Tailoring Strainer Solutions
Not all projects fit standard solutions. Engineers frequently require custom strainer designs tailored for unique flow rates, exotic media, hazardous environments, or stringent process certifications. Factors influencing bespoke strainer selection include:
- Required filtration level and particle size distribution
- Maximum allowable pressure drop at sustained flow
- Piping configuration and available footprint
- Material compatibility with process fluids
- Ease of maintenance access
- Compliance with international or industry-specific standards (ASME, API, PED, etc.)
Application Scenarios and Usage Cases for Types of Strainer in Piping
Strainer selection directly impacts operational performance and reliability. In power plants, basket strainers prevent turbine blade erosion by capturing scale and rust, enabling uptime rates above 99%. For chemical processing, duplex strainers are crucial—allowing for 24/7 operations where process interruption is untenable. In municipal water treatment, automatic self-cleaning strainers are routinely deployed, filtering millions of gallons daily and reducing filter cleaning labor-hours by up to 95%.
Case Example 1: A South American refinery upgraded from legacy Y-strainers to modern duplex basket strainers for its diesel transfer lines. The change reduced annual maintenance shutdowns from six to two, saved $120,000 annually in lost production, and extended pump lifespans by 25%.
Case Example 2: In a European food processing facility, the integration of self-cleaning strainers in the wash-water system resulted in a payback period of less than 18 months due to reduced downtime and manpower. Filter element service intervals jumped from weekly to nine months.
The diversity of pipe strainer types accommodates a spectrum of industry needs— from safeguarding high-precision microelectronics to supporting the daily operation of municipal water utilities. Leveraging data-driven selection, technical expertise, and intelligent design, organizations can achieve optimal filtration performance, regulatory compliance, and robust cost control across all applications.
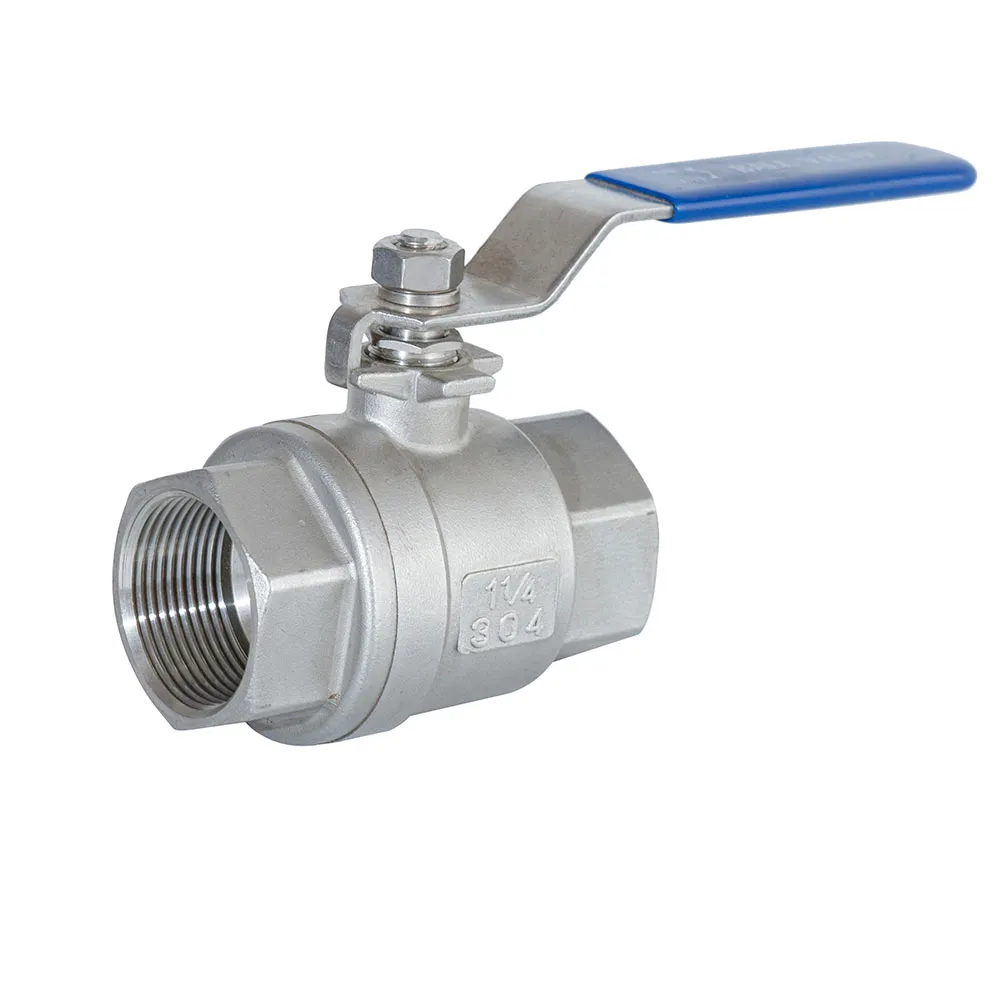
(strainer types in piping)